Propane industry invests in rail due to pipeline infrastructure issues
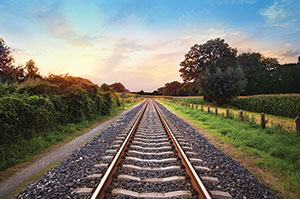
Companies are being driven toward rail, even though it’s not a foolproof solution. Photo: iStock.com/karinclaus
Propane is plentiful, but it isn’t easily available where and when it’s needed most. The preferred method to move the product is through a pipeline, but competitive forces rule out that possibility in a number of places across the country.
So what’s the next best option for an industry looking to move an energy product from one point to another in the United States? If you’re the propane industry, the next best option to which a number of companies are turning is rail.
“Rail is the less-preferred method,” says Jason Doyle, president of Alliance Energy Services, whose company is converting the propane terminal in Benson, Minn., from pipeline to rail. “We’re not getting into rail because we like it more than the pipeline. It’s purely out of necessity.”
Rail is more of a necessity now because existing pipelines are more congested with the demands of year-round products, says Mike Sloan, principal at ICF International. Sloan says all energy producers and midstream companies are scrambling to find opportunities to move their products and that the demand increase is putting tremendous stress on existing infrastructure.
“Companies are trying very hard to optimize the use of existing infrastructure, and when they’re building new infrastructure they’re building it for 365-day-a-year load as opposed to winter-peaking load,” Sloan says.
Pipeline reversals (i.e. Cochin Pipeline) and conversions (i.e. one of two pipes on the TEPPCO Pipeline) removed key sources that supplied millions of propane gallons to much of the Midwest. But, as Sloan points out, even pipelines that have not been reversed or converted are causing propane retailers pain.
“There’s been an increase in diluent headed up into the Midwest to feed the demand to go into Cochin and the other pipelines that go into Alberta, [Canada],” Sloan says. “That’s expected to continue over time.”
And so the pressure the propane industry is experiencing with the pipelines is driving a number of companies toward rail.
Assortment of concerns
Rail isn’t a foolproof solution, though. Other energy products present competitive challenges to propane on rail. Plus, rail has a history of unreliability – particularly during stormy winter months when propane is critically needed to heat homes.
“You can only load so many cars,” says Brad Box, energy division manager at Northern Star Cooperative Services in Deer River, Minn. “If you can load 30 cars a day seven days a week and today you only load 15, you can still only load 30 tomorrow. You can’t load 45. Once you’re behind, you stay behind the whole winter.”
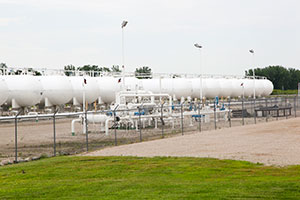
Alliance Energy Services finalized its acquisition of the Kinder Morgan Energy Partners LP propane terminal and related assets in Benson, Minn., where it has about 1.53 million gallons of available storage between 17 90,000-gallon tanks. Photo: Alliance Energy Services
Ron Batey, director of propane risk and asset development at CHS Inc., agrees rail presents unique challenges compared with other transport modes.
“You have to plan much, much more for rail than on a pipeline,” Batey says. “You have to plan how much it takes for the cars to get to the destination, how long it takes for the empties to return, and there’s managing the railcar fleet.”
Manifest trains hauling a variety of freight, including propane, also tend to slow service, Sloan adds.
“Say you have five railcars [of propane] and you want to drop it off in Wausau, Wis.,” he says. “You may start at the Tioga gas plant in North Dakota, but then those cars will get transferred between two or three trains. Cars get broken up and go to different locations. It’s a harder schedule.”
Rail’s scheduling challenges call for their own solutions. And the best solution to overcome rail’s shortfalls is more storage, Sloan says.
“To accommodate the change in reliability, marketers need to make a bigger commitment to wholesalers who commit to deliver propane on a reliable basis,” he says. “It means more planning and more looking ahead to make sure propane is available when marketers need it. It becomes a more complicated process in order to manage supply reliably when you’re using rail.”
Rail’s priorities
Competitive energy products – and even non-energy products – complicate matters with rail, as well. Rail companies, like pipeline companies, prefer steady, predictable loads, according to Sloan – an opportunity propane does not currently present throughout the year.
“We’re going to take a backseat to the bigger commodities, whether it’s grain or something else,” Box says. “We’re kind of at the mercy of the rail industry and the rail service. You hope for the best, but you prepare for the worst.”
According to Joe Rose, president of the Propane Gas Association of New England, the Northeast currently depends on about 75 percent of its propane supply from rail. Rail supplied about 15 percent of the region’s supply just a few years ago, he says. Sea-3 is looking to make its propane terminal in Newington, N.H., with 24 million gallons of available storage, rail accessible.
“At a conference last November I heard the vice president of Pan Am [Railways] say their volume had increased by 500 percent in three years,” Rose says. “I thought that was a very telling quote – and it’s not just them.”
The number of railcars available that are capable of transporting propane across the U.S. is an issue, as well. According to ICF International, the total North American pressurized railcar fleet capable of transporting propane consists of about 42,000 railcars. This fleet includes pressurized cars used for chemicals and other commodities.
Sloan estimates that about 8,000 of those 42,000 railcars are used to transport chemicals. The remaining cars are used for a variety of different energy products, including butane and ethane. After those products and others occupy cars, Sloan estimates about 14,000 railcars remain to transport propane.
“You could probably move 4,000 railcars back and forth between other segments – at least in the short term,” he says. “That happened quite a bit last winter. But when you take a car out of service, you either need storage [for the first product] or to figure out some other way to get that product to where it’s stored and used. That’s a challenge in a lot of places.”
The cost of switching out railcars in the short term is a pricey one, too.
“When prices go up, an economic incentive is the greatest facilitator,” Sloan says. “That’s what happened last winter. People realized they could put their railcar into consumer propane service and make enough money on the propane moved from point A to point B in order to make up for the money they would lose moving Y-mix from point A to point C.”
Still, switching out a few railcars for propane isn’t always economically viable for the railroads.
“That’s not how they can use their facilities most efficiently,” Sloan says.
Full steam ahead
Regardless of rail’s many issues, propane companies are making investments on the rail front to make up for pipeline losses. Alliance Energy Services, CHS and others are building rail infrastructure to aid the U.S. propane market.
CHS made a $24 million rail investment in five terminals across Minnesota, North Dakota and Wisconsin, Batey says, after exploring a number of potential solutions to overcome the loss of the Cochin Pipeline’s supply.
“We ran a big strategy study and looked at every way we could think of to do supply,” Batey says. “Should we build pipelines? Should we do rail terminals? Should we put in big storage depots? Rail was the practical solution because it could be done in a reasonable time period.”
Rail is also a more cost-effective solution than pipeline.
“The capital investment for rail is low,” Batey says. “It’s probably 1,200 miles between Edmonton, [Alberta, Canada], and Minneapolis. A pipeline costs about $1 million a mile to install, so a pipeline [from Edmonton to Minneapolis] is about a $1.2 billion investment.”
Rail has yet another advantage over pipeline.
“Rail allows us to get the right volumes near our customers, and in a lot of cases nearer to our customers because we got to pick sites,” Batey says. “We put terminals where our customers were centered, and we sized them to more than handle their normal supply needs.”
Alliance Energy Services’ new rail terminal in Benson, Minn., is sized to deliver between 30 and 40 percent of the volumes the Cochin Pipeline previously supplied on the same site, according to Doyle. The Benson terminal, which is expected to be operational come September, will be capable of unloading up to 32 railcars per day and storing about 1.53 million gallons.
“A lot of times what you see in building a rail terminal is very little storage,” Doyle says. “We liked [Benson] because it already had a significant amount of aboveground storage, which will allow us to give more reliable supply during potential rail delivery issues.”
Hess Corp. and Keyera Corp. are also making rail investments that should benefit the propane industry, Sloan adds. Hess is adding a rail facility in Tioga, N.D., to move natural gas liquids in the Bakken region to the Gulf Coast and other areas. Keyera is investing in rail in Fort Saskatchewan, Alberta, Canada, where the Cochin Pipeline previously started and flowed propane southward into the U.S.
Keyera’s rail infrastructure is not expected to be online until next year, though.
“That’s a concern for this winter in the Midwest,” Sloan says. “In other areas, I think the rail facilities that are going in are sufficient. The problem is with the reliability of the service. In order to account for the reliability changes, that really requires additional storage capacity.”
Some storage has been added across parts of the U.S. to make up for supply losses, Sloan adds, but he questions whether enough was added to maintain the level of reliability the industry expects to deliver to customers.
“Rail is part of the solution,” Sloan says. “It can’t be the whole solution. Rail has significant reliability issues that have to be addressed. It will fill in for some of the pipelines, but it’s not nearly as reliable as pipeline service.”
Batey is more optimistic about the industry’s ability to deliver propane effectively this winter.
“If the whole industry went from pipeline to rail, it would be a catastrophe,” Batey says. “But rail is part of the toolbox, and as long as we manage it well it’s a good tool to have.”
ABOUT THIS SPECIAL REPORT FROM LP GAS
The propane industry experienced one of the most challenging winter heating seasons on record in 2013-14. In preparation for future winters amid a changing energy environment, LP Gas is examining the issues that led to what some called a crisis supply situation. We are reaching out to all segments of the industry to explore our past and future, bringing attention to key subjects, initiating industry dialogue and providing necessary education to our readers.