Forklift safety takes center stage
The Industrial Truck Association’s (ITA) annual National Forklift Safety Day highlights critical forklift safety topics.
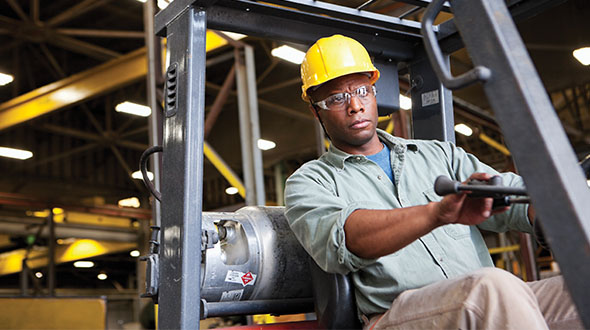
Forklift safety begins with trained employees who understand their job functions. (Photo: kali9/E+/Getty Images)
The educational program this year focused, in part, on the ongoing challenges of hiring, training and retaining warehouse and manufacturing labor. High rates of employee turnover, uncertainty associated with the COVID-19 pandemic and supply chain bottlenecks have all impacted facility safety, according to the ITA.
In observance of this year’s event, held June 14, the Propane Education & Research Council (PERC) hosted a webinar that addressed employee and customer training, regulatory compliance and equipment standards. Panelists included Mike Gioffre of American Cylinder Exchange and Jim Rushing of Energy Distribution Partners (EDP).
Employee training
Forklift safety begins with well-trained employees, according to Gioffre.
American Cylinder Exchange’s training program involves classroom or online learning and practical application, including an examination of a cylinder cutout showing the dip tube, valves and inner workings, and a drive-along with a fully trained employee.
The company also provides ongoing education and training for employees, such as skills assessments and monthly safety meetings, to ensure safe practices continue to be followed after initial training.
Whether they are drivers, dock workers or customer service representatives, employees are well trained when they understand all steps of their job functions and the “why” behind each of those steps, says Rushing.
“Why do we wear the gloves? Why do we wear face protection? Why do we have to check the date on every cylinder? Those are all important things [to do], and bad things can happen if you don’t, so we want to make sure [employees] understand that,” says Rushing.
Employers must also set clear standards by demonstrating key skills and reinforcing them over time: “You can’t cut corners. If you cut corners, [employees] are more apt to cut corners,” says Rushing.
Along the way, be sure to document all education, training and skills assessments to protect the company in the event of an accident.
“If you don’t document, it’s not done,” says Rushing.
Customer training
Training doesn’t stop with a propane operation’s employees. American Cylinder Exchange and EDP both offer training services for their forklift customers.
When American Cylinder Exchange onboards a forklift customer, it provides:
- On-site training.
- Safety booklet with key concepts and contact information.
- Video that demonstrates proper installation of a cylinder on a forklift truck.
- Visual inspection of the grounds to suggest safety measures such as crash posts for vehicular traffic, placement of cylinder rack, configuration of cylinders within the rack, and safety decals and signage.
Rushing suggests that the high standards applied to employees – explaining the “why,” reinforcing key skills and documenting training activity – should also be applied to customers.
This includes refresher training as needed, particularly if the company has an influx of new employees. It can be beneficial to train a trainer, such as a manager, at the customer location who can then train new employees, adds Rushing.
Customer communication
Effective communication about safety can support the business relationship a propane provider establishes with a forklift customer.
“When you pick up a customer, you’re partnering with that customer,” says Rushing. “You want that customer to know that you care about their business and the safety of their business and employees.”
That could mean providing additional resources to assist the customer in following best safety practices. In Rushing’s experience, those resources often include:
- Safety data sheets.
- Personal protection equipment like gloves and eye protection, within reason.
- Copies of training documentation for each employee trained.
- Duty to warn upon signing a new customer and annually thereafter.
- PERC brochures and resources like a scratch and sniff for detecting propane odor.