New agriculture technologies, more propane gallons
Agricultural applications use more than 825 million gallons of propane per year to heat water and buildings, dry or cure crops, power engines, and control pests.
Environmental restrictions, coupled with preferences to reduce chemical applications, are continuing to create opportunities for propane.
Many farm production and processing tasks require counter-seasonal or year-round fuel demand. One new application is a unique soil treatment machine developed by UC Davis researchers that uses propane-generated steam to pre-treat soil beds. Meanwhile, here are a few additional new technologies worth exploring for increased summer propane throughput in your operation.
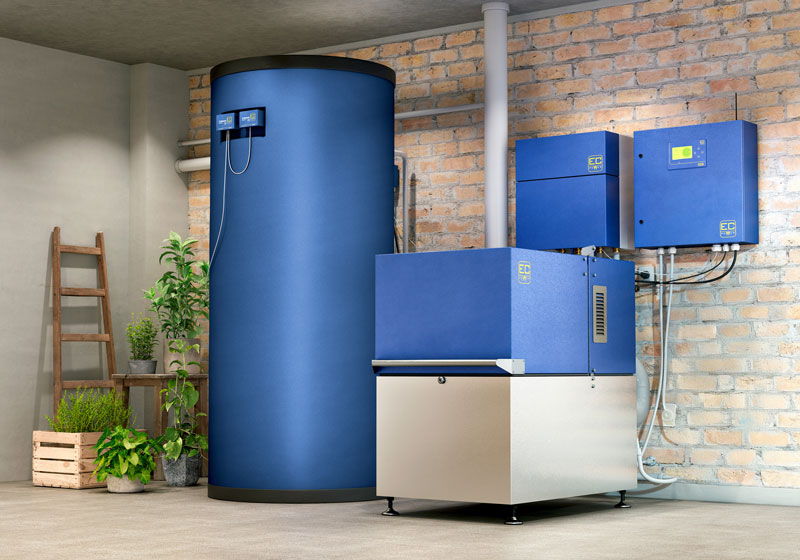
Combined heat and power
“The propane industry has a great opportunity to grow year-round demand through combined heat and power (CHP) applications and provide their customers with huge savings,” says Anders Thorsen, CEO of EC Power Inc.
EC Power has introduced a 24-kilowatt (kW) XRGI25 CHP technology to the United States. Based in Denmark, EC Power is a family-owned company that has placed over 15,000 units in 27 countries.
“The machine’s output can vary with demand and ranges from 12-24 kW in electrical power while also producing 112,000 to 163,000 Btu/hour in heat,” Thorsen says. “It’s an incredibly quiet technology at 49 decibels and is designed for continuous use and long life (40,000 hours), with a service interval of 4,000 hours.”
Propane marketers will enjoy the benefits of the machine in terms of year-round fuel consumption. It consumes between 2.0 and 3.2 gallons per hour of operation. At the midpoint, that’s about 62 gallons per day and over 22,000 gallons per year.
Blue Star Power Generation, based in Santa Rosa, California, has recognized the potential and recently signed a distributor agreement with EC Power to take the technology to end users in their markets.
“Ideal applications are those with continuous heat demands, such as agriculture processing, packaging, greenhouses or dairies,” Thorsen says. “Hotels, restaurants and multifamily housing applications are also great options.”
When the demand for heat and power exceeds the output of a single unit, multiple units can be cascaded together.
The XRGI25 has earned a high efficiency rating in Europe. Thermal efficiency is over 90 percent. Work is underway to obtain the equivalent ratings in the United States.
“In the future, we hope to bring both smaller and larger sizes to the U.S. along with additional features that will allow for ‘island’ operation and grid independence, which are currently in the works,” Thorsen says.
Irrigation and power generation
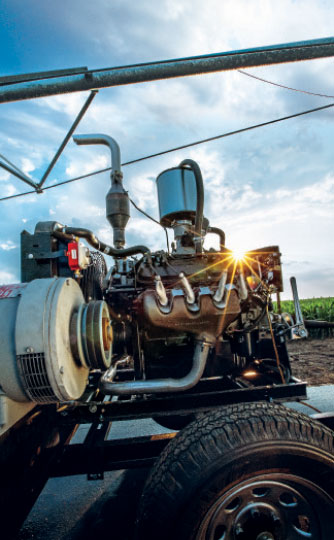
Industrial Irrigation in Hastings, Nebraska, has been providing industrial engines to agriculture and other markets since 1955.
“A 100-horsepower (hp) propane irrigation engine can consume 7.5 to 9 gallons of propane per hour,” says Jay Canada, vice president of Industrial Irrigation. “Annual hours of operation vary by region and crop, and range from 400 hours to 2,000 or more hours during the summer,” he says.
That’s 3,000 to 18,000 gallons of propane per year, for a 100-hp engine.
Because propane engines are an excellent option for crop producers, Industrial Irrigation has seen significant interest over the past 15 years.
“The time is right for propane engines, with diesel emission complexities and costs, combined with grid limitations for electricity,” Canada says.
Industrial Irrigation has embarked on a project, with support from the Propane Education & Research Council (PERC), to certify six new propane engines, ranging from 25 to 600 hp. The first of these to hit the market will be 2.4- and 3.4-liter inline four-cylinder models. They anticipate completion later this year, with four larger models under development in 2026. They will be marketed under their Reliable Horsepower brand.
“Applications for these engines include irrigation but also power generation, compressor pumps and other off-road uses,” Canada says. “All engines feature a heavy-duty block that is designed to meet the rigorous demands of agriculture and industrial applications.”
Propane is cost-effective, environmentally friendly and storable, making it an ideal fuel for irrigation and power generation applications on the farm.
“Propane engines can cost 20 to 40 percent less than a diesel equivalent, and the fuel savings can be significant,” he adds.
Flame weed control
Will Prull is the owner of FlameWerks in Eugene, Oregon, offering flame weed control equipment that features a fuel-efficient, contained flame. Equipment is modular and scalable for various applications.
“We’ve embarked on a project with PERC to test two of our new Flame Deck machines, each equipped with two multi-basket 3.0 burners. The project aims to reduce thatch buildup and control of mites in turfgrass,” Prull says. “We’ll be testing new burners that offer increased flame pattern adjustability as well.”
While flame weeding has been around for a long time, strong demand for organic foods, pesticide reduction and cost-saving opportunities are driving more farmers to add this equipment to their host of tools to manage weeds and pests.
“We see interest from farmers of all types. Some use it for spring and summer weed control; others use flame treatments to prepare for harvest,” Prull says.
Their flame weed control equipment can consume 4 to 28 gallons of propane per acre. The variance is due to the density of the area treated and the required speed of travel for efficacy. For example, an orchard or vineyard may treat just the area nearest the trees or vines, where wider row spacing is typical. Meanwhile, a turf farm would apply the treatment to the entire surface. The speed of travel and flame intensity vary according to the weed density or insect pressure.
One of the goals of the turfgrass flaming project is to nail down the best treatment protocols for turfgrasses in the southern United States. The testing will be conducted on Bermuda grass in Florida, late this summer and into the fall, with results by year’s end.
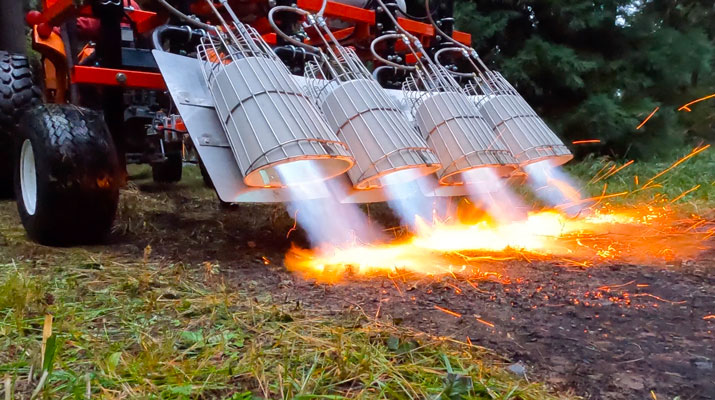
Other equipment and incentives
There are several additional manufacturers of CHP technology, propane engines and flame weed control equipment.
To see a listing of the additional providers of these technologies as well as other applications for the farm, visit propane.com. Under the “business use” tab, you’ll find a list of manufacturers for agricultural and power generation equipment.
There are a few helpful tools available here as well, such as irrigation and grain drying calculators.
PERC also offers a financial incentive for certain new technologies through the Propane Farm Research Program. Examples include $60/kW for prime power generators, $600/liter of displacement for agricultural engines and $1,500 for qualifying flame weed control equipment.
Mark Leitman is an 18-year veteran of the propane industry, having served many years leading agricultural and off-road programs for the Propane Education & Research Council. He most recently served as director of sales and Power Division director for Blue Star Gas on the West Coast. He currently works as a consultant and freelance writer for clients in the agricultural and energy sectors.