Propane prevails as reliable fuel during 2020-21 winter
Home cooking and outdoor living served up a heightened COVID-19 reality for propane retailers throughout this year’s winter heating season as customers stayed put and maintained social distancing.
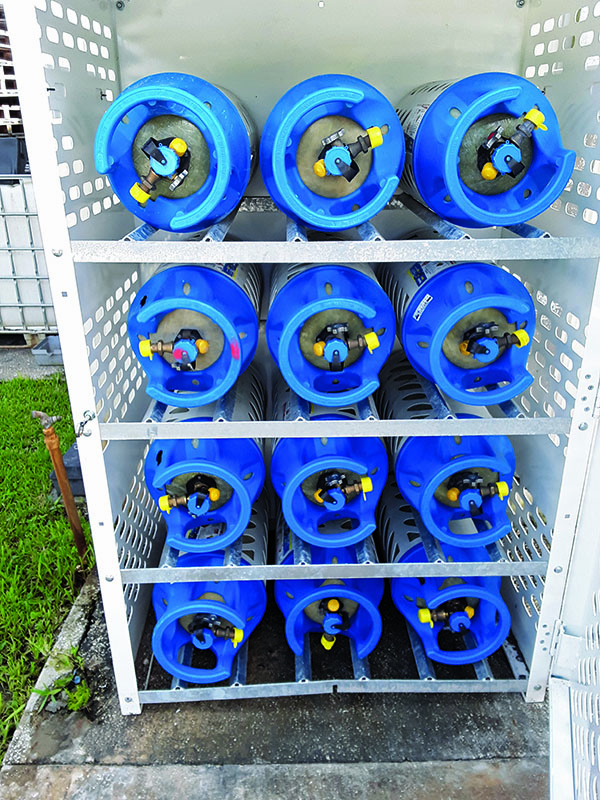
Due to the pandemic, many retailers experienced heightened demand from restaurants for their propane-fueled outdoor heaters. Photo courtesy of Propane Ninja
Sales of generators, grills, patio heaters and other propane appliances – plus the cylinders to power them – reflected the need to avoid contact with the coronavirus.
“All of these are through the roof,” says Mike Dodd, CEO of Propane Ninja, a cylinder exchange provider covering a 120-mile radius around Tampa, Florida.
“Restaurant patios were a must this past winter season, with most restaurants obtaining additional outdoor heating than usual,” he explains. “We sell to a great deal of restaurants, and demand has been staggering.”
Retail outlets such as convenience stores, hardware stores and supermarkets have demanded more bottle gas due to residents working from and spending more time at home; plus, many people have purchased propane-powered appliances for personal use outdoors, says Dodd.
“We have only seen growth in our markets since COVID-19 started,” he adds. “Industrial manufacturing was slow at first, but all markets have rebounded and are growing.”
In the “nesting” economy, people who are stuck at home want to invest in home improvement projects they’ve long dreamed about. As a result, hearth and barbecue sales have been “outstanding” during the pandemic, explains Bill Overbaugh, executive director of the New York Propane Gas Association (NYPGA).
“Companies that are well diversified were able to take advantage in a boom on this side of their business, which partially helped with a bust in the fuel sales side of the business due to the warmer winter [in New York],” says Overbaugh.
Proactive measures
Among industry leaders, a consensus has been reached that propane’s more traditional use as a home-heating fuel was executed effectively alongside COVID-19 relief.
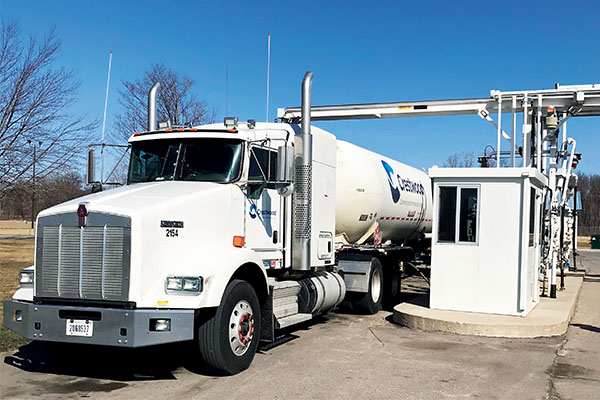
Crestwood integrated seven terminals from Plains All American into its operations. Photo by Steve Barnhart
“Generally speaking, the industry performed exceptionally well with little to no interruption of service,” says John Powell, senior vice president and head of marketing, supply and logistics at Crestwood Equity Partners.
“We noticed an increase in proper planning and coordinating amongst all players in the value chain,” he observes. “Most companies were much more proactive this year, greatly reducing a lot of the issues we typically see during extreme weather events as we had this year across many parts of the country.”
During the heating season, Crestwood successfully integrated into its existing operations its $160 million acquisition of seven terminals and four storage facilities from Plains All American. The enhanced systems provide “greater flexibility and surety of flow for both our producers as well as downstream markets,” says Powell.
Larger-than-normal draws
This winter’s supply and transportation scenarios went quite well with just a few exceptions, according to DD Alexander, president and owner of Global Gas. Alexander serves on the National Propane Gas Association’s (NPGA) board of directors, as well as NPGA’s Supply and Logistics Committee, Member Services Committee and Supply and Infrastructure Task Force.
Alexander says that, for the most part, the industry’s suppliers had enough gas available to meet retailers’ needs, and many retailers heeded the advice of NPGA’s summer webinars, which discussed what could be expected regarding possible transportation and supply scenarios.
“Many retailers were very diligent in lining up the proper supply commitments for the winter, and I think that showed,” she says.
As far as inventories, the industry saw very large builds last summer going into the fall, Alexander recounts. Then came larger-than-normal draws in the thick of the winter.
Inventories quickly went from surplus to below the 20-day supply level, which is considered the minimum among supply experts.
“In my opinion,” says Alexander, “with the inventories going so low, we may have a difficult time building our inventories back to where they were for the upcoming winter.”
Currently, she continues, experts predict the peak inventory will occur in October 2021 at about 90 million barrels – below last year’s peak of about 105 million barrels reached in September 2020.
“So far, for this supply season coming up, 2021-22, the producers are seeing less gas available for the domestic market in the Northeast and higher costs,” Alexander says. “Again, I think retailers would do well to contract early for their supply for next year.”
The new norm
Overcoming numerous operational challenges while also alleviating a sense of unease among the customer base during the pandemic has been a priority across the industry.
At Paraco Gas, based in New York, the team has embraced several new safety protocols – such as the addition of personal protective equipment, enhanced sanitization, staggered shifts, working from home and contactless deliveries – all to ensure that the company can continue serving its customers without delays.
“Now that we have these COVID practices in place, it has become the new norm,” notes Jeff Ruffner, Paraco’s executive vice president of operations.
The biggest issue the company faced was situations where customers ran out of gas and the need arose to conduct a leak check, says Ruffner. Customers also had to be assured that employees entering their homes were following Centers for Disease Control and Prevention (CDC) guidelines and Paraco’s enhanced COVID-19 safety protocols.
“This caused some minor delays as we spent more time with customers to ensure they felt comfortable, and we also had to rework employees’ schedules to occasionally send a different employee to put the customer back in service,” Ruffner says.
Paraco had to develop a COVID-19 strategy earlier than many companies, as the town of New Rochelle, New York, turned out to be an early epicenter for the outbreak.
“Having a distribution location within a few miles provided us with the benefits of being able to react quickly and work on a crisis management strategy immediately before many other areas were impacted,” explains Christina Armentano, Paraco’s executive vice president of sales and business development. “We found ourselves getting a jump start on identifying how we can protect our customers and our employees.”
The company formed an internal COVID-19 task force to work on a crisis management strategy and communicate as conditions changed, says Armentano. Understanding the CDC guidelines became a critical component to educating employees who had been exposed to COVID-19.
‘Hit early and hit hard’
In this time of national stress and tragedy, Overbaugh of NYPGA is quick to remind everyone that “we have an incredibly resilient industry that benefits from traditional American values of hard work and dedication to customer service. I’ve witnessed businesses reassess how they manage their operations, shift to remote working as much as possible, and implement backup and fail-safe measures from a personnel standpoint. In a lot of ways, these unfortunate circumstances have pushed our industry to reassess our business processes to ensure uninterrupted supply to customers, and in that way, we will be a stronger industry when this is over.”
The Empire State “was hit early and hit hard by COVID-19,” says Overbaugh. “Our governor put measures in place very early to stop the spread of the virus. Some of those measures have been criticized as being draconian, but there’s no doubt that they have also been successful. It changed the way many of our members conduct business inside their offices.
“I know many suppliers and retailers whose businesses have been hit by COVID-19 and who stumbled, but none who fell down,” he adds. “I think most members have been able to shift resources around to provide continued service.”
As for heating consumption, New York’s winter was warmer than average, and volumes were down across the state.
“Propane supply in the Northeast is greatly impacted by anything that impacts Mont Belvieu, Texas,” says Overbaugh. “The situation in Texas did lead to a significant spike in spot pricing in our market. I am not aware of anyone being unable to source product, though, only having to deal with the run-up in short-term pricing.”
A Texas-sized mess
Propane came to the rescue for many residents of Texas when the Lone Star State was buffeted by exceptionally nasty and rare winter storms that sparked cascading statewide power outages.
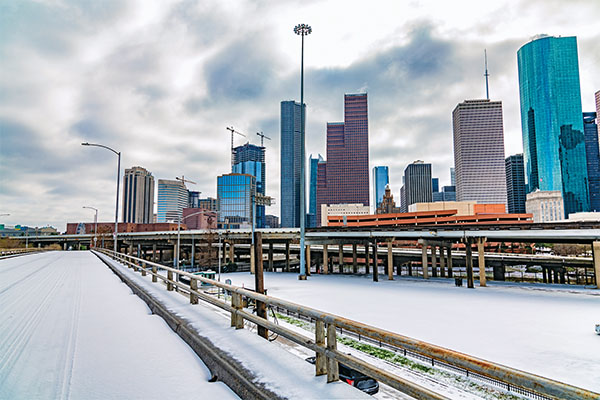
Throughout harsh winters and weather crises, such as what Texas faced this year, propane serves as a dependable energy source. Photo: Art Wager/iStock / Getty Images Plus/Getty Images
Texas has its own electrical grid – not connected to any other state’s power grid – managed by ERCOT, the Electric Reliability Council of Texas. “An ironic name for the agency that failed so miserably,” muses Bill Van Hoy, executive director of the Texas Propane Gas Association.
No electricity meant no water in many locales, and the gas plants could not produce or pump.
“The propane industry is no stranger to challenges,” he says. “Every drop must in some way be transported to the end user: ice, snow, sleet, driver fatigue, hours of service, fractionation plants going offline, supply points being backed up – all were challenges with which this industry had to contend.”
Pumps, meters and associated apparatus were unable to function. Gas stations, too, were out of order, with dispensers idled by the outages. The trucking industry suppliers were overwhelmed with demand.
“Add it all up, and it comes down to doing the best with what you have available,” says Van Hoy. “Every single individual in the process had to make tough calls, from front-office staff to the driver on the road; each industry member had to be on their game. There were out-of-gas situations, of course, but it’s all about how our industry handled it: From my perspective, we stepped up to the challenge.”
For the first time on record, the National Weather Service issued winter storm warnings for all 254 counties in Texas. The power grid’s failure impacted 5.2 million homes and businesses, the vast majority in Texas, and the event became one of the largest blackouts in modern U.S. history.
“I don’t think anybody was prepared enough for what we experienced because it was record-breaking,” says J.R. Anderson, marketing manager at Dallas-based Gas Equipment Co. (GEC).
Yet a number of propane providers were indeed equipped with generators, as was Anderson.
Because of previous weather-related crises and blackouts, he “recognized the value of proactively investing in backup generators” for both GEC locations, including the corporate office. Due to that foresight, “we were fully functional, and the only challenge our customers experienced was the freight companies suspending their operations temporarily,” he notes. “Some of our customers utilized will-call – picking up equipment at our warehouses – and our traveling sales representatives supported customers by personally delivering equipment.”
Says Josh McAdams of Shelby County’s McAdams Propane: “Propane has prevailed as a key energy source during this event.”