Technology to train drivers, manage risk
Propane marketers manage risk on a day-to-day – even minute-by-minute – basis when they send out their drivers to transport or deliver fuel, or perform any number of functions in a vehicle.
“You have driver meetings and toolbox talks, and you try to make sure everybody’s on the same page and being safe, but once they leave your yard, you don’t really know what’s going on out there,” explains Randy Benson, general manager at Sapp Bros. Petroleum, based in Omaha, Nebraska.
Sapp Bros. and Paraco Gas are two propane retailers that turned to technology to take some of the unknown out of managing those risks and ensuring driver safety.
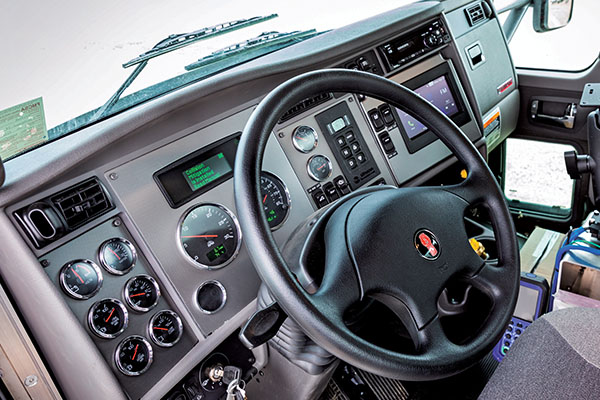
Collision mitigation systems are designed to reduce human error and react faster to certain dangers than drivers. Photo courtesy of Westmor Industries
Driver assistance tech
Sapp Bros. identified following distance as one major risk, says Benson. The company implemented collision mitigation technology several years ago to help ensure its drivers keep a safe distance.
Collision mitigation systems encompass a variety of functions such as:
- Visible and audible alerts to warn drivers of forward-collision hazards, including unsafe following distance or stationary objects
- Lane departure warnings.
- Adaptive cruise control that sets a specific following distance.
- Automatic emergency braking, which can prevent accidents or reduce the impact of an imminent collision.
The technology is designed to reduce human error and react faster to a dangerous situation than a driver.
That’s not to say the technology can’t fail. Benson says Sapp Bros. has experienced some downtime, as well as associated costs and repairs, when a system throws an error code or otherwise malfunctions.
He nevertheless emphasizes the technology has continued to evolve and improve during the four to five years Sapp Bros. has used it: “Every time we buy a new piece of equipment with it on it, it’s a little more advanced and works a little better every time.”
Performance of the technology is just one of several factors retailers assess when determining the return on investment. Retailers also weigh the cost of the technology against the cost of past accidents, and consider vehicles and driving situations where the technology would be most beneficial, says Jason Soulon, regional sales manager at Westmor Industries.
Vehicles that operate primarily on high-speed roads and highways, like transports, tend to see the greatest return on investment for collision mitigation systems, explains Soulon. Depending on the operation, though, bobtails and service vehicles may also be good candidates.
Retrofitting vehicles in phases can help retailers manage the cost of new technology. Paraco Gas, based in Rye Brook, New York, installed collision mitigation systems on its 12 transports and will use the transport fleet as a model to determine whether its bobtails and service trucks would benefit from the technology, explains Dave Latourell, director of safety and transportation.
Coaching drivers
For Paraco, a cookie-cutter approach to driver safety can’t address the many types of driving employees engage in – from metro New York City to rural areas – or the different vehicles they control. Paraco’s approach instead focuses on teaching drivers awareness so they can make good decisions on the road, says Latourell.
“We expect [our drivers] to be developing their skill set and taking advantage of training,” says Latourell. “And we try to offer them a variety of different training tools to hopefully try to emphasize the opportunity areas.”
Collision mitigation systems serve as one tool to improve habits: “Appropriate and timely activations could reduce distraction, modify driver behavior, teach drivers how to identify conflicts before they unfold and enable improved vehicle control,” says Soulon of forward-collision warnings.
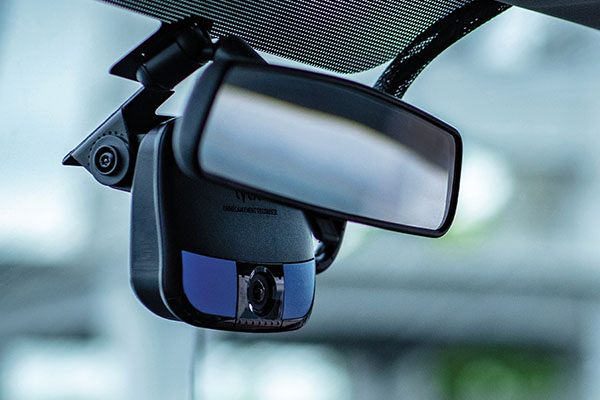
Drive-cam technology can help managers reward good driving behavior and coach risky behavior. Photo courtesy of Lytx
For Paraco and Sapp Bros., drive cams serve as another tool. Both retailers partnered with Lytx – a provider of event recording, fleet tracking and compliance services – to add another source of information when assessing risk and training drivers.
Lytx event recorders capture video footage in front of the vehicle and inside the cab. As the camera rolls, machine vision and artificial intelligence identify unsafe situations like close following distance or sudden swerves, as well as risky behaviors like using hand-held cellphones or failing to wear a seat belt. Lytx also provides human review of footage to pick up on subtleties such as failure to scan an intersection, explains Del Lisk, vice president of safety services at Lytx. Video clips of flagged events are available on an online platform so clients can review the footage and share it with drivers.
Paraco initially installed the technology at the recommendation of its insurance carrier so video evidence could be used to determine the cause of an accident, explains Latourell. But the company also views the service as an opportunity to coach drivers.
“Even our best drivers have habits or opportunities where distracted driving can create a problem,” he says.
To improve following distance, Sapp Bros. combined the capabilities of collision mitigation systems and Lytx data, ranking measurable improvements in distance against the number of coachable events flagged by Lytx month over month, explains Benson.
For both companies, proper rollout and management of drive-cam technology has been key.
Because supervisors at propane operations tend to wear many hats, says Lisk, some marketers have expressed difficulties with managing workflow and keeping up with the need for monitoring and coaching.
But in Latourell’s view, investing time in a review process should already be a part of a robust safety program.
“You’re always going to have to go back and review and guide because complacencies always slide in,” he says.
Driver acceptance of the drive cams can also present a challenge if drivers feel they are being policed.
To alleviate these worries, Sapp Bros. and Paraco clearly communicate to employees that the technology supports them.
For one, drivers can be rewarded for good behavior that may otherwise go unseen.
“Maybe another driver pulled out in front of one of our propane company drivers – they were alert, they were attentive, they responded immediately and safely – we would see that video, too, and that would be an opportunity for a client to call out a driver for doing a great job,” explains Lisk.
Video footage may also exonerate propane drivers in the event of an accident. Sapp Bros. has used Lytx footage to clear its drivers of blame in several instances, says Benson.
“It’s a culture change that says this tool here is to support you, to help you improve habits … because in the instance of an issue or an accident, there’s just as high a likelihood that the camera will vindicate that the driver is doing everything properly,” says Latourell.
Safety sensors
Mike VanDenBoom, president of Signature Truck Systems, says he is seeing more independent propane marketers ask for safety features such as pull-away protection and crane truck sensors. These technologies detect whether a hose, crane or outrigger is properly stowed, and can prevent the driver from moving the vehicle until appropriate steps are taken.
Use of such safeties can extend to many different parts of the truck, says VanDenBoom. For example, sensors can be installed on chock block holders or even cabinet doors to ensure drivers store chock blocks or close doors before moving the truck.
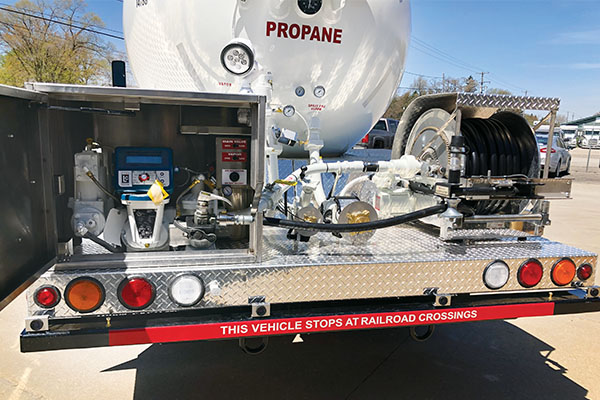
On this bobtail, Marshall Excelsior safeties are installed on the spray fill line, vapor equalization line and hose end nozzle stow. Photo courtesy of Signature Truck Systems