Trucks: Supply chain disruptions extend lead times, raise prices
For propane truck manufacturers and the marketers they serve, the unpredictable has become the familiar.
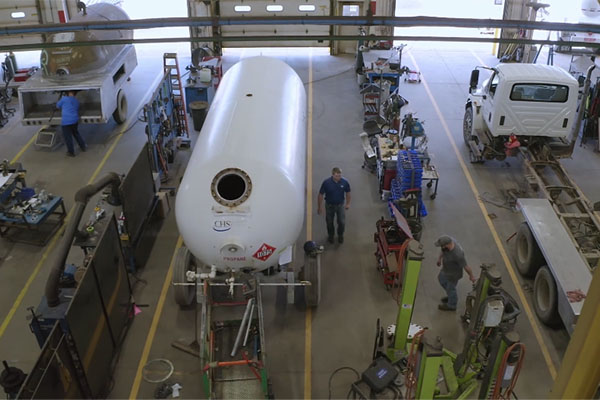
Production schedules at Westmor’s shop are in constant flux due to part shortages. (Photo courtesy of Westmor Industries)
Two years after the COVID-19 pandemic triggered supply chain disruptions in the automotive industry, Mike VanDenBoom, president of Signature Truck Systems, says he’s almost gotten used to the delays.
“We’re becoming numb,” he says when asked what truck parts have been the most difficult to source. “We just expect to probably have delays and just bought everything we touch.”
He spends a lot more time on the phone with suppliers these days to assess when materials will arrive at his facilities and anticipate shortages. But schedules are difficult to predict.
“In the past, we would get an order, and I could, at that point, pretty much estimate when we may complete it based on previous lead times,” says VanDenBoom. “Today, we might get the order, and then we have to go research for sure how long it’s going to take to get the components, and then establish a completion date, and then communicate that back to the customer.”
Maintaining a consistent workflow amid the uncertainty means carrying more inventory and following flexible build schedules that take into account when different parts are expected to arrive. While lead times vary widely depending on the component, VanDenBoom has made it his mantra to prepare to wait twice as long for parts: “We’re using that thought process every day as we’re needing to order parts and up our inventory.”
He estimates inventory is 20 percent to 30 percent higher than normal for this time of year.
The uncertainty around when and what materials will be delayed also complicates inventory and production schedules for Westmor Industries, says Jason Soulon, sales manager. On any given day, delays may affect many different parts, from chassis to meters to hose reels.
To compensate, the company is carrying more inventory, but those warehouse commitments require more capital.
“We’ve increased our commitments for chassis, raw materials and equipment to provide larger buffers in our production schedule, but demand is still outpacing supply,” says Soulon.
Trouble with chassis
Propane truck manufacturers agree: Of the many parts and components delayed by supply chain issues, extended lead times on chassis cause the most trouble. They’re hearing from chassis manufacturers that a microchip shortage is expected to persist for the foreseeable future, limiting chassis supplies.
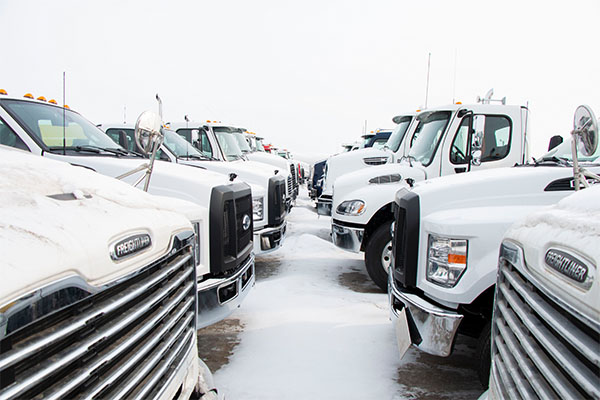
Propane truck manufacturers are seeing long lead times for chassis due to a microchip shortage. (Photo courtesy of Westmor Industries)
At Signature Trucks, VanDenBoom sees lead times on some truck parts improving but can’t say the same for chassis: “In the case of chassis now, that’s not improving at all. Chassis are still 12 to 18 months out.”
Fisk Tank Carrier, which builds custom trucks and trailers, requires different chassis sizes for different models. Yet, chassis manufacturers like Ford, Dodge and Chevy have been unable to confirm what size chassis they will send to fulfill Fisk’s orders, says Nathan Roberts, president of Fisk.
Without knowing what size chassis will be available, he can’t forecast what models to build, which makes it harder to sell the units, he adds.
Roberts says he doesn’t expect the situation to improve this year, so he’s planning 18 months out to ensure an adequate supply.
Westmor has had to get creative to deal with the short supply, says Soulon. It is buying chassis from more truck dealerships than usual and has introduced new products to help marketers avoid the long wait, including a chassis-less trailer that can be attached to a marketer’s existing chassis assets.
By the end of April, Westmor had sold all of its chassis and were selling into next year, says Mandi Carlberg, marketing communications manager.
Volatile prices
And it’s not just chassis. Supply chain disruptions in multiple industries are delaying deliveries and hiking prices for automotive raw materials and components across the board.
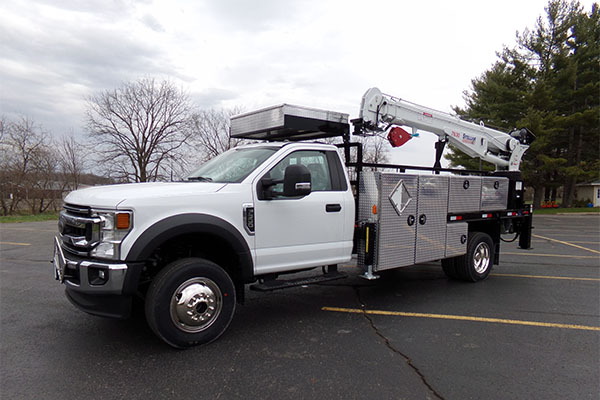
Aluminum and steel raw material prices remain high. (Photo courtesy of H&H Sales Co. Inc.)
While H&H Sales Co. has secured a steady supply of steel and aluminum, prices are high and change frequently, says Philip Randall, president of the company.
“If you get a quote for aluminum or steel products that we use in our manufacturing, then you’re lucky to get a week out of that,” he says. “You better get it ordered in a week, or it’s going to have to be quoted again.”
Randall observes similarly volatile prices for petroleum-based products like tubing, mud flaps and fenderettes.
He says raw material prices have more than doubled for some of the products H&H Sales makes, and when price increases can’t be absorbed, the customer may see anywhere from a 25 percent to 35 percent price increase.
Like H&H Sales, Signature Truck hasn’t been affected by shortages of steel and aluminum but has had to pass on higher prices to customers.
“The end user is feeling most of the pain from increasing prices,” reports VanDenBoom.
Plan ahead
Randall says he doesn’t expect supply disruptions to end for another 12 to 18 months, to give a rough estimate.
Within the next 12 months, Randall and VanDenBoom expect marketers to request more service and repair work on older trucks to avoid a price premium on new trucks or to ensure they have an operable vehicle right away, instead of waiting a year or more for a new model.
Still, some marketers will find they need a new truck regardless.
“If you can find a truck, then you need to buy it,” says VanDenBoom. “Because there’s not many options open. Inventory is low for new trucks.”
VanDenBoom recommends marketers look ahead 1 1/2 to two years to anticipate their fleet needs and start planning for those needs now.
Watch list
Among the raw materials and components for which propane truck manufacturers report supply disruptions or high prices are:
- Aluminum
- Axles
- Chassis
- Fenderettes
- Hose reels
- Hydraulics
- Meters
- Mud flaps
- Steel
- Tires
- Tubing
- Winches
From point A to point B
Factoring into the long lead times for propane trucks are delays in transporting a truck that’s completed, and often paid for, from the manufacturing site to the marketer’s location.
The drive-away companies that typically handle the transport are experiencing driver shortages, leading to long waits for truck deliveries, explains Mike VanDenBoom, president of Signature Truck Systems.
“Sometimes we have trucks completed and sitting in a yard for four months waiting for a driver to pick it up,” he says.
These drive-away companies also handle the title process and license plates for the vehicle, so backups at the Department of Motor Vehicles are contributing to the problem.
VanDenBoom says Signature Trucks has three transport trailers on the road.
“Our drivers are very busy delivering new trucks, but we don’t have our drivers do that licensing process,” he explains.