3 essential protocols for interruption-of-service calls
As cold weather envelops regions across the country, propane companies can expect more frequent interruption-of-service situations. Interruption-of-service calls, often referred to as out-of-gas calls or IOS calls, may be caused by an empty tank, gas leak, equipment failure, inaccurate delivery schedule or increased gas demand caused by weather.
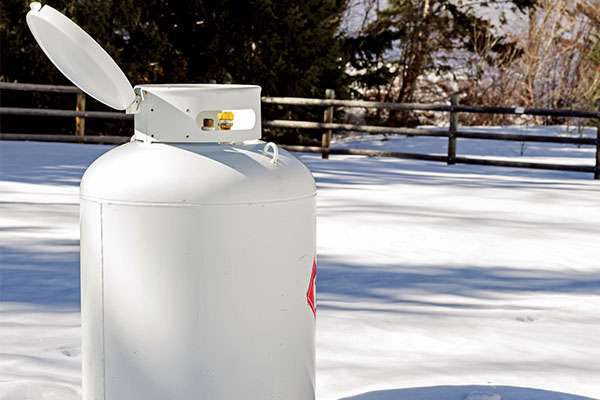
Winter often brings more interruption-of-service calls. (Photo: knowlesgallery/iStock / Getty Images Plus/Getty Images)
Regardless of the reason for the call, every propane company must have a proper protocol to ensure that interruption-of-service situations are handled correctly. Is your team prepared for interruption-of-service calls this winter? Read on to learn three things you need to maintain compliance, keep everyone safe and reduce risk.
Proper protocol
1. Policies and procedures: Every propane company needs a written policy regarding interruption-of-service calls. Do you have written procedures for staff? Written policies and procedures should include a customer service representative (CSR) script and procedures for a suspected leak response team. Review and update these procedures annually prior to the season’s start.
2. Accurate documentation: You’ve heard it before: If it isn’t documented, it didn’t happen. Properly documenting interruption-of-service calls and how your team responded is crucial to protect your company and the employee performing the work in case of litigation.
3. Updated employee training: When a customer reports an interruption of service, your customer service team is the first point of contact. It is crucial that CSRs are trained to handle interruption of service. Additionally, initial training and annual refreshers are crucial for the company’s drivers and technicians who respond to and remedy these scenarios.
How does your company protocol for interruption-of-service situations stack up? Making sure you have all three elements listed here in your safety program will help your team operate efficiently while protecting your customers, employees and company.
Wes Sheppard is the senior consultant of safety and training at P3 Propane Safety. He has 30-plus years of experience in safety management and corporate instruction positions. Reach him at wes_sheppard@p3propanesafety.com.
NOTE: The opinions and viewpoints expressed herein are solely the author’s and should in no way be interpreted as those of LP Gas magazine or any of its staff members.
From the field
Propane retailers tell LP Gas about the safety culture at their companies during the 2022 LP Gas Growth Summit.
LP Gas: What are some of the steps your company takes to ensure the safety of your employees and customers?
Steve Brown, Texas Star Propane: “We strive with our employees to follow all of the rules and regulations. Propane is a very safe product, but it has to be treated with respect. Foremost for us is the safety of our employees – to make sure everybody goes home in the evening to their families.”
Carl Kiedrowski, Country Visions Cooperative (Wisconsin): “Through the Wisconsin Propane Gas Association, we have hired a trainer who has a trailer that is set up to train new employees. The trailer has appliances built in for doing safety tests. We usually bring him in to do those safety trainings, but we [also] keep everybody up to date on their CETP training. We use an informative video series that we launched through Facebook and some other avenues to keep the customers informed on topics we get questions on a lot.”