Avoiding propane tank placement issues
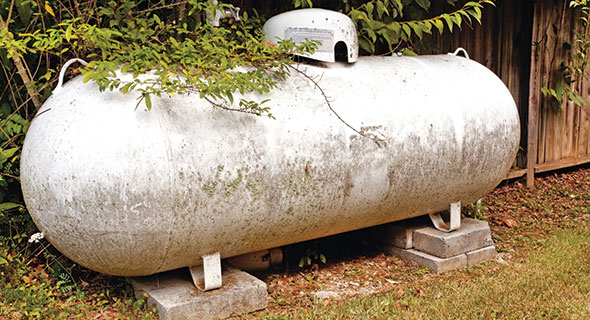
Tank placement code violations tend to occur when marketers deliver to customer-owned tanks. Unless the code violation is obvious, it is often ignored. (Photo: Joe_Potato/iStock /Getty Images Plus/Getty Images)
Of the many claims and lawsuits arising from propane fires and explosions, the majority of them focus on tank placement issues.
In the rare case, the tank is placed in clear violation of the code and contributes to the ensuing fire or explosion. Yet it is more often the case that the tank code violation does not contribute to the gas leak but is used to place the propane marketer in a bad light. The goal in this is to get in front of a sympathetic jury that will award large sums to a badly injured plaintiff or someone who has suffered a significant property loss.
Tank placement code violations tend to occur when marketers deliver to customer-owned tanks. Unless the code violation is obvious, it is often ignored. Some code violations also occur when the marketer is the entity that sets the tank.
It is common that after an incident we find the tank is not a full 10 ft. from any important building, adjacent containers or adjoining property line that can be built upon. It may be 9.5 ft. from the important building and did not contribute to the event, but the violation will still be used to suggest a lack of concern for safety.
We also see data plates on ASME tanks that are difficult to read. This is a code requirement for ASME tanks. We find that the tank has always been used for propane, but if the data plate is not legible it is a strike against the marketer, as the code says it should not be filled. So, check the data plate and be sure it is legible. Take a photo of it on first delivery to document its condition.
Cylinders are often found out of certification while still in service. These cylinders are rarely a cause of gas leaks but feed the lack-of-adherence-to-safe-practices theme. It is also valuable to document which cylinders you fill. We find that many marketers fail to identify the actual cylinder they fill. So, when a claim is brought, they cannot prove that they did not fill the subject cylinder.
A rare issue is the requirement under Section 6.3.1.1 of NFPA 58 (2014) that the tank be 10 ft. from the adjoining property line upon which a home could be built. This applies to 150- to 500-gallon tanks. The distance varies per the size of the tank. The point often missed is the tank setback requirement is from adjoining property. If the adjoining homeowner can build up to 5 ft. from his property line, a 500-gallon tank needs to be at least 5 ft. off the property line upon which it is set, which equates to 10 ft. This is in addition to being at least 10 ft. from any significant building or another 150- to 500-gallon tank. When setting a tank or going to fill a customer-owned tank for the first time, you need to verify that the tank build-out setback requirements have been met. The homeowner should have the lot setbacks on a plat that he can share with you.
Another code violation is when the cylinder or tank is too close to an opening below the discharge point. Cylinders must be 3 ft. horizontally from a relief valve that may discharge to an opening below it. For ASME tanks, the distance must be 5 ft. horizontally from the relief valve discharge to an opening below it. If the discharge could be from a relief valve, vent discharge or filling connection to an exterior source of ignition, the distance must be at least 5 ft. for cylinders and 10 ft. for ASME tanks to any direct-vent appliances and mechanical ventilation air intakes.
We also see aboveground LP gas containers that are set within 6 ft. of overhead electric power lines that are more than 600 volts nominal. This is a violation of Section 6.4.4.13 of NFPA 58 (2014).
We rarely see these types of tank and cylinder placement issues cause gas leaks and subsequent fires, but they do cause static that can keep otherwise defensible cases alive.
Read more: Avoid common code violations when installing propane containers
John V. McCoy is with McCoy Leavitt Laskey LLC, and his firm represents industry members nationally. He can be reached at 262-522-7007 or jmccoy@MLLlaw.com.