Field Tank Services thrives by installing, servicing monitors
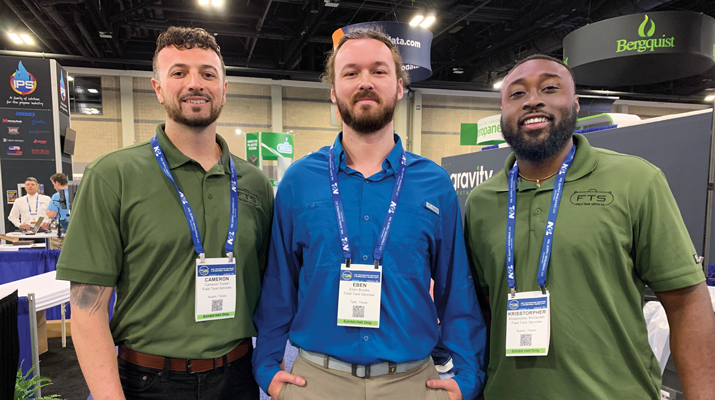
Eben Brooks cites the phrase multiple times during the conversation.
His opportunity in the propane industry, even the company he launched to carry out his work, was the result of him being “in the right place at the right time.”
Brooks was doing “handyman work” in 2019 before he met someone in the propane industry involved in tank monitor installation pilot projects. Working with tank monitors piqued his interest, and it led him to form Field Tank Services, a company that deploys and maintains tank monitors.
But the first big project began with an eerie feeling. Brooks and his small team at the time took a flight to Florida in early 2020, at the outset of the COVID-19 pandemic, and he recalls only four other passengers on the plane.
“It was one of the first things we did during that time,” he says. “We were lucky that with COVID, we were still able to do a lot of work. We’re outside and not interacting with people too much, [just] saying ‘hello’ at the door.”
Nearly five years later, Field Tank Services is going strong, having installed more than 100,000 monitors and growing to about 25 total employees. It’s a sign of success for the company but also a positive sign for an industry that continues to adopt technology to serve its retail propane customers.
“It’s like when you buy a new car,” Brooks says. “You never saw that car on the road, and then you buy the car and now you see it everywhere. Every time I see a propane tank, I’m looking to see if there’s a monitor on it. It’s encouraging to see more and more.”
Field Tank Services has experienced an uptick in business over the past two years, stemming from a customer’s large installation program. The company, which works with tank monitor providers and propane retailers, installed about 10,000 monitors in three-and-a-half months.
“We’ve been growing steadily, and we’re in a good spot now,” Brooks says. “We’re handling the work that we have with the team that we have.”
The Field Tank Services team is spread across the country, with a greater concentration in the Midwest and East, says Brooks, adding that employees are willing to travel to customer locations to take on a job.
Here’s a look at how the company operates – and other key factors:
Installation
“If you need a large deployment, and you need it done quickly, that’s where we come in,” Brooks says. “If a company bought 200 monitors, we’ll help them out, but they can probably do that themselves. Most of the smaller companies I’ve talked to, they’re using monitors, but they don’t need help installing them.”
When Field Tank Services undertakes a job and arrives at a customer location, the tank monitor installation process unfolds in a straightforward way, Brooks says.
“From the time we say ‘hello’ to the homeowner and get the install done, it shouldn’t take more than 15 minutes, and on average you’re probably looking at under 10 minutes,” he says.
Brooks explains further, “We’ll replace a dial if needed, plug in the monitor, secure it to the feed line and set it up on the tank. There are some apps involved with whatever monitor we’re dealing with. It’s not a long process at all.”
Depending on the area and the density of a route, Field Tank Services employees each expect to install about 25 monitors a day, Brooks notes.
Safety and training
Though installation is straightforward and short in duration, Field Tank Services works to ensure a safe process, using both in-field training and video training to educate its employees.
“The biggest thing we push is safety,” Brooks says. “We don’t do anything that could potentially cause an unsafe situation, and most of the time that’s not possible because we’re not messing with the internals of the tank.”
The biggest point of emphasis during training is ensuring that employees understand the different types of dials used on the tanks, Brooks says.
“There are quite a few that look similar but are used in different situations,” he adds.
Service
In addition to tank monitor installation and setup, Field Tank Services says it can replace and repair monitors that need service.
“Currently we are doing quite a bit of service work,” says Brooks, estimating that service makes up about 40 percent of its focus and expecting that number to increase as the industry uses more tank monitors.
The company has addressed communication issues with monitors, stuck float gauges or replaced batteries or sensors. Brooks sees its offerings continuing to move in this direction.
“It’s going to be more of a regional approach and having technicians spread out to where the service work is more feasible,” he says. “That’s the movement forward – a more regional approach and focusing on the service aspect of things. That seems to be where we can continue to thrive – on the service end.”
Looking ahead
Propane tank monitor installations comprise about 95 percent of the company’s work, Brooks says, but business on the oil side is also growing.
Smaller projects could contribute to the overall picture for Field Tank Services; whether the company undertakes these types of projects would depend on their location and its available resources in the area.
Brooks, however, is thinking big.
“Bigger picture is bigger projects and service,” he says.
Brooks attended his first Southeastern & International Propane Expo last year in Charlotte, North Carolina, alongside Field Tank Services’ Cameron Tucker and Krisstorpher McDaniels.
Brooks called the experience of seeing technology on display at the show “encouraging.” It only reinforced the direction he’s taken Field Tank Services over the past five years.
“We started small, and we’ve grown and implemented systems. We’ve done some incredible things,” he says. “We’ve been able to retain a lot of people and not have a lot of turnover. I can’t give enough praise to my team.”