How to handle a premature valve closure
The safe transfer of LPG in and out of large tanks on trailers or on truck chassis is critical to the LPG industry.
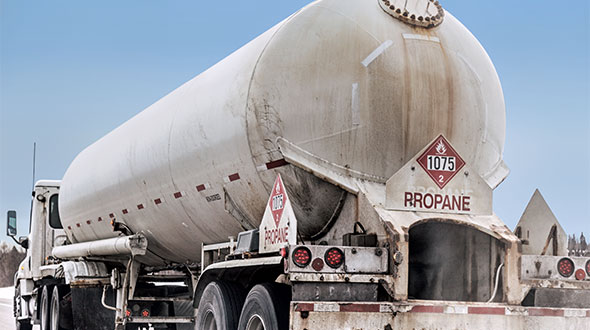
The safe transfer of LPG in and out of large tanks or on truck chassis is critical to the LPG industry. Photo: iStock.com/skhoward
A key step in such transfers is the opening and closing of the tank’s internal valve. This article offers a more operator friendly sub-system for the opening and closing of this internal valve that is more cost-effective in the long term, as well as safe.
Too frequently the operator/driver of the trailer/tanker faces this dilemma: You just opened the liquid internal valve to unload your trailer or storage tank and started your pump, but the 427-2 liquid internal valve or the 404 liquid internal valve (depending on what is installed) slams shut.
This sudden closure prevents any product flow, and this condition will last until the pressure on both sides of the valve equalizes. This lengthy pressure-equalization process can cause extensive (and expensive) delays and may also damage the pump. Further, the slamming of the internal valve shortens its life.
Prevention method
Industry practice to prevent this internal valve from snapping shut is to install a system including an air regulator that lowers the pressure to the actuator system from 120 pounds per square inch (psi) to about 60 psi. The pressure drop activates the internal valve actuator, which allows the internal valve to open. This regulator and the pressure valve are typically located under the trailer on the main air tank.
Years of hands-on practice indicate that this system may not always function as intended. Experience with thousands of such product deliveries has shown that the air regulator can fail (slamming the internal valve shut), and much time and significant dollars are spent to troubleshoot and repair this system. Worse, such failures may occur when the load delivery is time-sensitive and/or when the weather turns ugly.
Most trailer manufacturers now use off-the-shelf Department of Transportation (DOT) air brake chambers to actuate the liquid internal valve. These air chambers are designed to use 120 psi air pressure and can operate for thousands of cycles. Manufacturers are now building their actuators with the air supply at a much higher pressure.
But using 120 psi air may cause premature closure due to the rapid actuation of the internal valve. Further, the shift to 120 psi pressure may also cause the internal valve to take longer to close than what DOT standards allow time-wise to complete its closing in an emergency. This higher-pressure shutting down process takes longer because of the greater volume of air at high pressure that must be bled off.
Another option
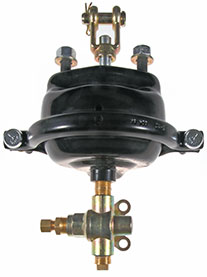
A 1512 Weatherhead piloted orifice and 7800 Sealco valve assembled and installed on an air chamber to be attached to an internal valve. Photo by Daniel Hernandez
The offered option below addresses several of the issues mentioned above. And it does so with off-the-shelf parts sold at most truck supply stores.
It consists of adding in front of the air chamber a 1512 Weatherhead piloted orifice to a 7800 Sealco quick air dump valve, along with suitable bushings and adapters. The piloted orifice allows the internal valve to open slowly, while the quick air dump valve allows the liquid internal valve to close fast enough to stay within the minimum time allotted by DOT. This approach allows for 120 psi throughout the system, including the operation of the internal valve actuator.
Also, having a higher air pressure to activate the air chamber holds the added safety benefit that, in the event of a fire, the lead-sink (thermal fuse) will blow out sooner.
The suggested system is relatively easy to install, but remember this key point: It is imperative to install the exhaust port on the Sealco quick air dump valve pointing down and toward the rear of the vehicle to keep out unwanted road grime and debris. Further, to keep out debris in severe service conditions, an air suppressor may be added to the discharge port.
Following its design over 15 years ago, this approach has been successfully used on a system with a 427-2-in. liquid internal valve or with a 404 liquid internal valve.
The system described here may be a little more expensive than the one including a pressure regulator, but doing away with the wasted time and cost of field repairs – plus the avoided inconvenience of such repairs – should easily make up the difference over time.
Ernie Reed has more than 40 years of experience in the LPG industry and in the transport of hazardous materials. His work experience includes management as well as technical positions.
AUTHOR’S NOTE: Important notice and disclaimer of liability: Any such modifications on a trailer or in a tank farm must be reviewed and approved in writing by all appropriate safety directors and/or maintenance managers. The author makes no warranties and assumes no legal responsibility for the completeness, reliability or accuracy of the information contained in this article. Any action taken based on the information in this article is at one’s own risk, and the author shall not be held liable for any losses or damages that may result from the use of such information.
EDITOR’S NOTE: The opinions and viewpoints expressed herein are solely the author’s and should in no way be interpreted as those of LP Gas magazine or any of its staff members.