Injury cost estimator underscores importance of a safety culture
I took an Occupational Safety and Health Administration (OSHA) training class recently that would help an owner determine how much it might cost their company to cover certain accidents. Maybe that approach will turn an owner’s head so they can see how the lack of a safety culture or attitude could ruin them.
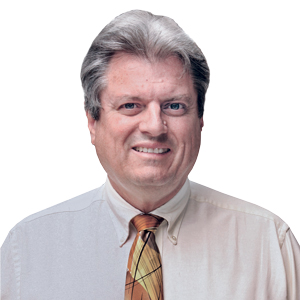
I took OSHA 7505, “Introduction to incident [accident] investigation,” shortly after the National Propane Gas Association’s Southeastern & International Propane Expo. The convention had me pumped up about safety because of some great sessions about a “safety culture” concept for helping to reduce accidents.
The OSHA class focuses on the safety culture concept, but with a twist not familiar to me: cost. OSHA has a “$afety Pays” tool. You select from a variety of injuries, enter a value about profit margin and see what it might cost your company because of that injury. I can’t speak to the accuracy of the tool, but the trainer thought it was good.
Burns are a significant possibility in this industry, so let’s see how this tool deals with burns. We’ll also explore loss of vision, a real possibility if someone gets a face full of propane liquid because they didn’t wear their eye protection. I’m sure there is a wide variation in the real-world costs, but this claims to show averages. Be sure to read the disclaimer if you use the tool.
I selected one burn incident that harmed one person and used the default 3 percent profit margin. If it’s likely that more than one person gets hurt, make adjustments.
The tool responded with average costs of:
- Direct cost of $47,192
- Indirect cost of $51,911
- Total cost of $99,103
- Additional sales of $3,303,433 required to offset this total cost.
A company can buy a lot of fire-resistant (FR) clothing that can potentially prevent a single burn incident for a lot less than $99,000. Outfitting its entire hazardous area staff with FR clothing would probably be well under this amount. And how long would it take to return to profitability after covering that loss with more than $3 million in sales? Think of the anguish possibly prevented, which really doesn’t have a monetary value. However, juries often have grand ideas about what it’s worth.
What about loss of vision? Again, I used the defaults. The tool responded with:
- Direct cost of $75,885
- Indirect cost of $83,473
- Total cost of $159,358
- Additional sales of $5,311,933 required to offset this total cost.
Loss of vision is a significantly more expensive accident than a burn. Also, it’s easier and cheaper to provide eye protection that can prevent or significantly reduce the likelihood of an employee losing their sight.
One question in particular prompted some deeper thought concerning liability: “Are incidents always unplanned?” The answer was, “Knowing there are ways to avoid an incident and not doing them makes an incident ‘planned.’” Is it a legal requirement to take actions to avoid incidents – to make standard plans to avoid or mitigate an incident before it happens? Based on the findings of many court cases where hefty fines and compensation were mandated, I would say yes. But you might not find such explicit language in the general statutes.
These seminars and training stimulated my thinking about the importance of a safety culture in the propane industry. It’s a high-altitude look at the overall situations that can develop into incidents. This high-altitude view must be taken by the owners, managers and supervisors and relayed to employees as one of the most important parts of their job. Many people consider safety to be more than a priority. It’s a core value.
Our inspectors see many situations where employees fail to perform certain required steps for examining a cylinder before they fill it. They also see bobtails and transports parked without wheel stops because the driver was “in a hurry” or “stepping only a short distance away” or “forgot this time, for the first time.” If owners and supervisors stress that shortcuts of rules to save time are not permitted, maybe employees will realize that “taking care of Number One” really is good business, even if it takes a little longer.
Richard Fredenburg is an LP gas engineer at the North Carolina Department of Agriculture and Consumer Services, Standards Division. He is also a member of NFPA’s Technical Committee on LP Gases. Contact him at richard.fredenburg@ncagr.gov or 984-236-4752.
NOTE: The opinions and viewpoints expressed herein are solely the author’s and should in no way be interpreted as those of LP Gas magazine or any of its staff members.
Featured homepage image: bluekite/E+/Getty Images
Related Articles
Training your employees and documenting your training