New unloading system offers heating season solutions
Rail terminal operators know that when they unload propane, a few hundred gallons of product are left behind in each rail car.
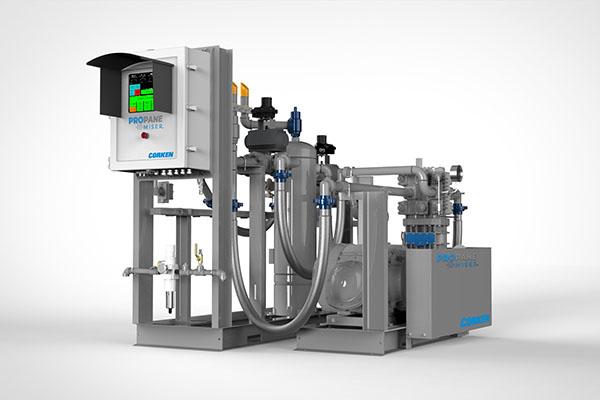
Photo courtesy of Corken
The Propane Miser, a new unloading system by Corken, delivers a solution to that problem.
The Propane Miser’s PLC-controlled, two-stage compressor design allows terminal operators to safely evacuate all of the propane from a rail car down to 0 psig, says Steve Willoughby, global business director at IDEX, the parent company of Corken.
“When you start to look at the amount of propane that people pay for that they don’t receive, that’s actually on the order of magnitude of 1 percent,” says Willoughby. “So what that means is if somebody is getting 100 rail cars into their terminal, one of those rail cars isn’t actually getting into the terminal.”
Corken tested the Propane Miser in the field with alpha customers for more than six months, making observations and modifying the design to the current version on the market today.
The final product gives rail terminal operators several features for unloading propane, says Willoughby:
The system can unload the same amount of propane 25 percent faster than rates observed previously.
Or, in the standard amount of time, it can unload an additional 150 gallons of propane.
Over a longer period, the compressor’s algorithm determines when to enter “deep vapor recovery mode” to evacuate all of the propane, recovering about 200 to 400 additional gallons per rail car.
Heating season solution
With the busy season approaching, these options can help terminal operators move product faster and secure additional gallons to sell during peak demand periods.
“When we talk about the savings from this unit, we’re really talking about it in terms of the cost you save on the propane,” says Willoughby. “In a supply-constrained environment, those savings would obviously be higher because now you’re looking at lost sales.”
The unit’s touchscreen controller also allows operators to make adjustments on the fly – as quickly as one evacuation to the next – depending on the strain of any potential backlogs, says Dan Clevenger, strategic markets manager.
For those operators who are reluctant to make a change in operations as the busy season begins, Corken offers assisted setup on a case-by-case basis, with partners located regionally, says Clevenger.
Engineers involved in the development of the compressor are also available to answer questions and provide support.
Furthermore, the system’s all-in-one design makes it easy to install – it comes on two skids with all of the controls, automation and proprietary technology included, says Willoughby.
Annual savings vary, but operators can expect to save a couple hundred thousand dollars a year on average and see a return on investment in about one to two years, says Willoughby. Corken developed a savings calculator that terminal operators can use to determine their expected savings based on the pressure at which they were unloading rail cars, the new pressure they’d like to unload to, the number of rail cars they unload per year and the cost of propane.