Propane containers play key role in safe system operation
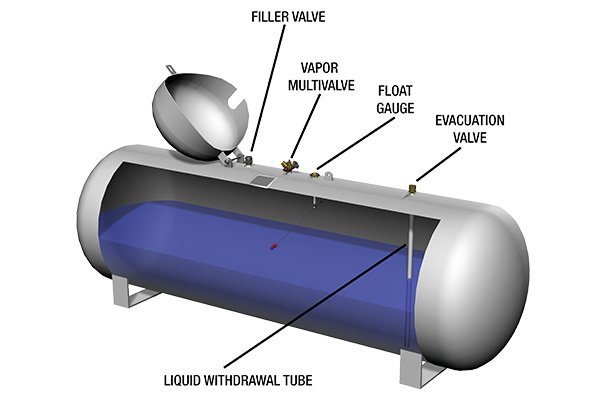
Diagram courtesy of the Propane Education & Research Council
Spring is in the air. It is the time of year when everyone is glad to have survived another winter and starts to look at what the rest of the year will bring.
I want to discuss just how important propane containers are in the propane system. You have heard me talk about the regulator as the “heart” of the propane system, and I think the container could be considered the “lungs” of the propane system.
Why do I say “container” instead of “tank” or “cylinder”? To put it simply, “tanks” typically are built to American Society of Mechanical Engineers standards, and “cylinders” typically are built to Department of Transportation standards. To avoid getting into the exceptions and explanations of each, I use the generic word “container,” which could refer to either one.
A container has several components, which all play a role in the container’s safe operation. There are some variances in how containers are fitted with components. Below are some typical components found on containers:
- Fill valve: Provides the attachment point from the delivery truck and has a safety feature that only allows flow into the tank, referred to as a back check.
- Relief valve: Safety valve that monitors the container’s pressure and allows excess pressure to vent in an over-pressure situation.
- Service valve: The primary way propane vapor is released from the container.
- Float gauge: Indicates the liquid level in a container, typically expressed by percent of container size.
- Fixed liquid level gauge: This device is a fixed tube designed specifically for the type and size of container. It indicates maximum allowable liquid level in a container, typically at 80 to 85 percent of container size.
The container provides vapor to the propane distribution system, which provides the appliance with the fuel it needs to operate. It does this through a process called vaporization. Vaporization occurs when the liquid propane boils, creating propane vapor. The container needs to be sized properly to provide enough propane vapor.
The vaporization rate of containers is determined by the size of the container’s surface area, which dissipates the energy to create the vapor.
There are other things to consider when sizing a container, such as expected outside temperatures; the lowest expected quantity of liquid in the container for the expected load; and where the container will be placed at the customer location. The container provides the fuel to the vapor distribution system like our lungs provide oxygen to our blood cells to distribute in our bloodstream.
The Propane Education & Research Council (PERC) provides excellent educational material in Designing and Installing Vapor Distribution Systems, which can be accessed through the PERC Learning Center at propane.com.
The designs of most of the container components have not changed over time, but, as technology continues to evolve, innovations have emerged:
- Fill valves have incorporated low emissions and Euro-style connectors.
- Relief valves have incorporated new technologies.
- There are new ways to determine the level in a container.
- Even the fixed liquid level gauge has been updated with a smaller orifice size to reduce emissions when used during the filling process.
The containers themselves are likely to evolve over time. The composite cylinder is an example of this, and I think we will soon see advances in container construction for automotive and marine applications.
All of the industry innovations and advances of the components and containers will continue to provide a reliable, efficient and safe means to provide propane vapor to the propane distribution system.
Randy Warner is the product safety manager for Cavagna North America. He can be reached at randywarner@us.cavagnagroup.com.
NOTE: The opinions and viewpoints expressed herein are solely the author’s and should in no way be interpreted as those of LP Gas magazine or any of its staff members.