Understanding the heart of the propane system
I typically write about personal safety, but in this article, I take a different approach and talk about a key element of safety within a typical residential propane system, the propane regulator.
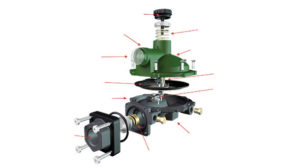
Image courtesy of Cavagna
The purpose of the regulator is to control the flow of gas vapor from the container to the burner tip. The regulator ensures safety by providing over-pressure protection, usually by means of a pressure relief device. This is why we often refer to the regulator as the heart of the propane system.
Types of propane regulators
There are many different types of regulators designed to fit different applications. Sizing a regulator correctly for the load on the system is very important. Types of regulators used in residential applications include:
First stage (high pressure) – Typically placed at the container and decreases the container pressure to 10 psi.
Second stage (low pressure) – Typically placed at the residence and decreases the pressure from the first-stage regulator to inches of water column (often 11).
Integral two-stage (twin) – Some smaller load systems can bring container pressure down to inches of water column with a regulator that has both stages built in, sometimes referred to as a twin-stage or piggyback regulator.
Automatic changeover – Similar to an integral two-stage regulator in regard to pressure regulation but also has a mechanism that allows it to monitor vapor pressure switching from one tank to another in a multi-tank installation. Read more: Understand automatic changeover regulators
Two pound – Placed at the residence and decreases the pressure from first-stage regulator to 2 pounds. Used in newer systems where the gas vapor demand requires additional regulation before the appliance.
Line (appliance) – Placed before the appliance and decreases the pressure from 2 pounds to inches of water column (often 11). Does not have integral relief and usually uses a vent limiter.
What makes a regulator?
While features vary among manufacturers, the basic components are the same in most regulators. The main parts of a regulator include:
Body – The main physical part of the regulator, typically the lower portion.
Cover – The upper part of the body, color coded for its type of service. For example, red can indicate high pressure.
Inlet and outlet ports – The inlet is where gas vapor enters the regulator and the outlet is where it exits the regulator.
Orifice – Determines the amount of vapor that can pass into the regulator.
Lever – As the flow of vapor passes the orifice, the lever pushes up on the diaphragm.
Diaphragm – Senses pressure and starts and stops the flow of gas vapor.
Main spring – Provides tension on the diaphragm to regulate flow.
Relief – If excess pressure flow beyond the capacity of the regulator occurs, the relief mechanism (spring) allows the propane vapor to exit through the relief valve. This prevents excess pressure from building.
Vent – Built into the cover, allowing the regulator to breathe during normal operation. Vents can also be placed where the relief mechanism discharges.
Vent screen – Keeps debris from entering the regulator.
Dust cap – Allows you to see into the cover, retainer nut and main spring.
Never attempt to modify, manipulate or repair regulators unless you are qualified to do so and have approval from the manufacturer.
Because the regulator is the heart of the propane system and is the key element in ensuring safety, it is important to understand how it works. The Certified Employee Training Program and the consumer education materials provided by the Propane Education & Research Council are excellent sources of information.
Randy Warner is product safety manager for Cavagna North America.
NOTE: The opinions and viewpoints expressed herein are solely the author’s and should in no way be interpreted as those of LP Gas magazine or any of its staff members.