Propane protects Fisher Vineyards from grid disruptions
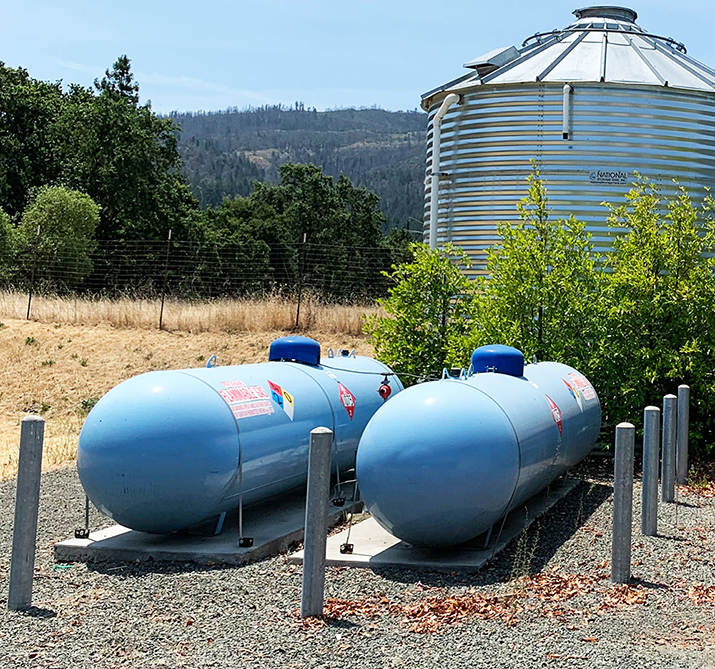
Two 1,000-gallon tanks sit behind the winery at Fisher Vineyards in Calistoga, California. (Photo by LP Gas staff)
Northern California wine country offers a delicate balance of rolling hills and flatlands. This part of the country is pleasing to the eyes – and to the tastebuds.
But before the fruit of business labor produces the sought-after food and drink emanating from this region, moving onto a plate or into a glass for enjoyment and nourishment, the agriculture producers and growers must ensure their possessions and processes are guarded from the elements and from the risks that surround them.
For, as beautiful as the region presents to those who reside here and visit, dangers remain: Extreme weather, wildfires, power outages. For a business that bases everything on time and temperature, successful outcomes are met within a short window.
Fisher Vineyards knows this all too well. Based in Santa Rosa, California, with estates in Napa Valley (Calistoga) and Sonoma County (Mayacamas Mountains), the family winery has felt the frustrations of power disruptions over the years.
“We need a lot of power, and harvest tends to be at the peak of grid disruption,” explains Fisher Vineyards CEO Rob Fisher, second-generation owner of the winery with his sisters, Cameron and Whitney. “We felt that in a big way in 2017, 2019, 2020. Every time we have a critical process, we’re losing power.”
Fortunately for Fisher Vineyards, Santa Rosa-based Blue Star Gas serves as a friendly neighbor that can relate to the conditions that businesses, especially those in agriculture, face in California. Equally important, Blue Star Gas launched a dedicated power division in 2021. So, when Fisher Vineyards sought a solution to its power struggles, it partnered with a propane marketer with the know-how to keep the winery running in the toughest of times.
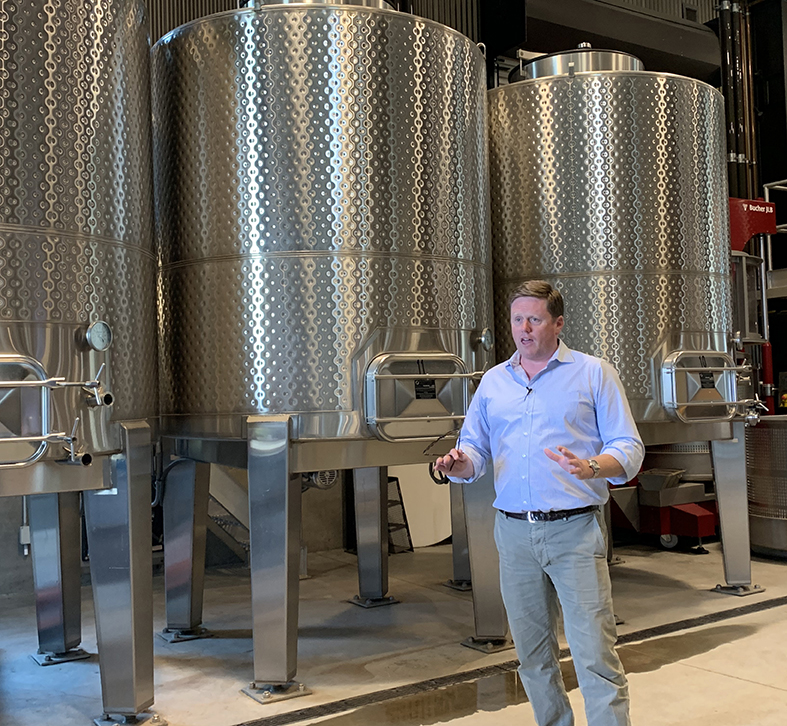
Propane can power fermentation tanks during a grid outage or wildfire evacuation. (Photo by LP Gas staff)
A need for power
Wildfires, public safety power shutoffs and other grid stability issues in California were the driving force behind Blue Star Gas’ formation of its power division several years ago. Mark Leitman served as its first director and had been part of the working relationship with Fisher Vineyards.
While Leitman no longer works for Blue Star Gas, he still underscores the importance of such a division in California. He was employed at Blue Star Gas during Fisher Vineyards’ foray into backup power generation.
“I saw us grow a lot in the wine area over my seven-year period,” says Leitman, describing propane applications in wine country such as space heating, water heating, wind machines and backup power, including for irrigation pumps.
“There was demand for that over the last few years because of the instability of the power grid,” he adds, also recalling a 10-day power outage at his house. “A lot was driven by the wildfires that were more common than we had hoped.”
In the process of working with Blue Star Gas for its propane needs – two 1,000-gallon propane tanks sit behind the winery – Fisher Vineyards learned how propane could serve as a reliable backup power source. As Rob Fisher says, the business can’t operate without reliable power.
During a June tour of Fisher Vineyards’ Calistoga Estate, with a wildfire burning 25 miles to the northwest, Fisher describes the winemaking processes, propane’s role across their two locations and how it can help to maintain those processes during power failures. In addition to the backup power generation applications, Fisher Vineyards uses propane for water heating, material handling and its HVAC systems.
Fisher explains the complex fermentation process, noting how propane can play a part in temperature control. He also describes a networked system of pumps under each fermentation tank that can run automatically on backup power during an evacuation.
There is no wiggle room with winemaking. Power outages could spoil the product, which is why the propane-powered generator would work when called upon to keep the barrel cellar at a consistent 55 degrees.
Fisher adds perspective by describing how the full value of the harvest is going through the production processes during a 30- to 45-day window. So, he not only thinks about cost-efficiencies of the processes but the value of risk mitigation amid a forced evacuation or power outage.
“It isn’t just the harvest season too,” he says, also noting the “mission critical” timing involved in bottling the wines. “We have winter storms with lightning and other events that have shut down power. It’s throughout the year.”
That’s why the partnership with Blue Star Gas was so important.
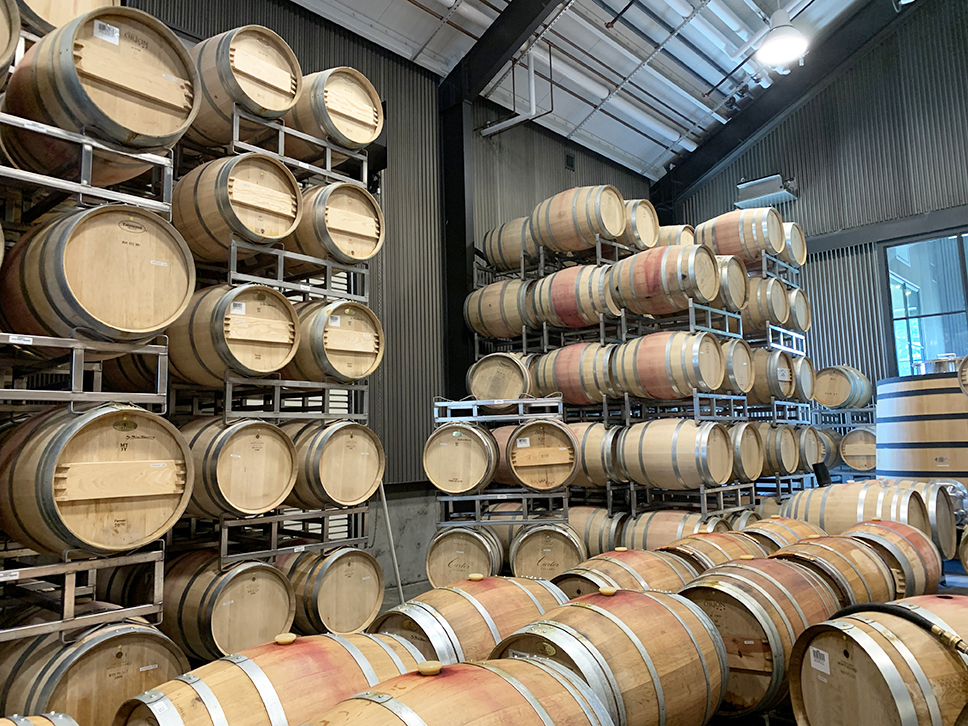
Propane backup power ensures the vineyard’s barrel cellar maintains a consistent 55 degrees. (Photo by LP Gas staff)
Propane marketer expertise
Blue Star Gas installed a 150-kW propane-fueled Kohler generator behind the winery in November 2021, about two months after installing a 24-kW generator at the house fronting the vineyard. The house also has a 500-gallon propane tank.
“One of the most crucial pieces to their service was their assistance with their engineering – first the source of the generator itself and the expertise in terms of certain permitting as well as the local subsidies for it,” Fisher explains of Blue Star Gas’ role with the large-scale generator.
“If it were left for me, it would have been more heavy lifting, but to have an integrated service provider that was able to help me on the equipment, installation and permits, and any funding programs, was really great.”
Installing such a system, Leitman says, allowed Fisher Vineyards to forego annual rental expenses and portable diesel units while taking advantage of propane on-site.
Leitman marvels at the Kohler unit, which uses a PSI 8.8-liter engine. The versatile unit is also sized accordingly so that it could pump water from nearby sources for fire protection, if needed. He says the generator could burn about 11 gallons of propane per hour at 50 percent load and 15 gallons per hour at 75 percent load.
“Keep in mind you are in one of the most air quality sensitive districts in the country,” Leitman says. “Napa Valley and most of the Santa Rosa territory [are] under the Bay Area Air Quality Management [District], so larger generators like that have to be permitted through the Bay Area. It’s good we have clean-burning propane products that can obtain certification through the Bay Area, so that was my job – I led them through that application process to get Bay Area permitting.”
The permitting process can be arduous and costly. Fisher Vineyards benefited from the Propane Education & Research Council’s (PERC) Double Propane Farm Incentive Program. It provides a financial incentive up to $10,000 toward the purchase of new propane-powered farm equipment. In exchange, participants agree to share real-world performance data with PERC.
“Because of these environmental problems, these catastrophes, every little extra support helps ensure the project goes propane rather than diesel,” Leitman says.
Adds David Lee, Blue Star Gas’ current power division director, “Here in California, where emissions are a really big deal, most temporary generation is done with diesel. If we were to offset that with propane, it can have a really big impact.”
Because Fisher Vineyards chose to expand its use of propane by installing the generator system, it received PERC’s Energy for Everyone Hero Award. Mike Newland, director of agriculture business development for PERC; Trent Nagata of Blue Star Gas; and Colin Sueyres of the Western Propane Gas Association were among those at the Calistoga Estate in June for the award presentation.
Fisher accepted the award from Newland and described propane as reliable, efficient and clean.
“It’s everything that we need,” he says. “We’ve been through a lot of really challenging years. We hope for easier years going forward. I know we’re set to face those challenges for many years to come.”
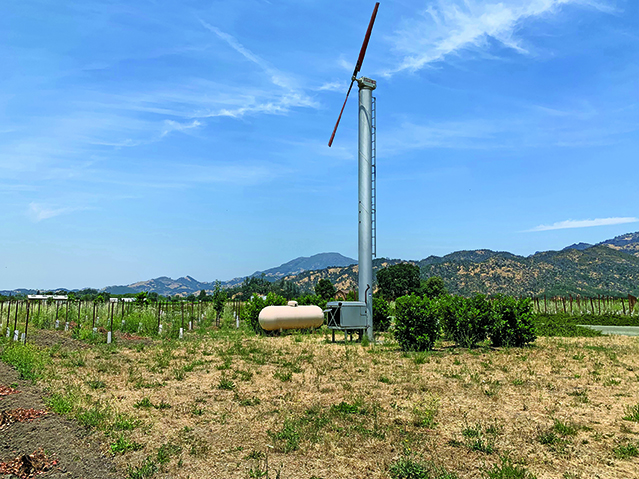
Propane-powered fans at Fisher Vineyards prevent the cold air from settling in one place as the vines are coming out of dormancy. (Photo by LP Gas staff)
Propane fuels frost prevention fans
Propane tanks dot the 60-acre landscape of Fisher Vineyards’ Calistoga Estate. Each of the four frost prevention fans at this location is fueled by a 500-gallon propane tank. Their purpose is simple: to prevent the cold air from settling in one place as the vines are coming out of dormancy.
“On the valley floor, we have the challenge of cold air collecting in the basin,” says Rob Fisher, CEO of Fisher Vineyards.
The fans are needed seasonally, often from mid-March to mid-April, as temperatures drop below 38 degrees, Fisher says.
Using propane for this application is a natural fit, he adds, because it’s not possible to run powerlines throughout the vineyards.
The fans don’t run often, but when they do, everyone knows.
“I live at the front, and when you wake up, it sounds like you’re on an airport,” says Cameron Fisher, who oversees sales and marketing for the winery.
Elsewhere in California
While spending time in California in June, the Propane Education & Research Council (PERC) celebrated another achievement.
Prior to honoring Fisher Vineyards with the Energy for Everyone Hero Award in Santa Rosa, PERC representatives were farther south in Salinas watching a propane-fueled soil steam applicator in action. It’s been operational since March.
PERC helped fund the project by approving a docket in 2022 totaling about $600,000, allowing council partners to build a commercial steam unit for use in vegetable, strawberry and flower production. The unit, using steam to control soil nematodes and weed seeds, aims to help farmers displace diesel and replace toxic fumigants.
PERC has been working with Steve Fennimore, an extension specialist in University of California, Davis’ Department of Plant Sciences, on the project. He specializes in weed management for vegetables, flowers and strawberries.
Mike Newland, director of agriculture business development for PERC, reports positive results from the visit.
“We were watching the unit in the field operate as intended,” he says. “The technology, the recipe, is a very proven recipe for controlling weeds, the soil nematodes that can impact vegetable plants in a negative way. We were thrilled with the results.”
Newland says propane is powering the soil steam applicator’s Kubota engine and producing the steam. He estimates the unit will burn about 900 gallons of propane an acre for lettuce production and about 1,500 gallons an acre for strawberry production, which has a deeper steam injection point.
He also envisions the soil steam unit making its way across the country as a benefit to high-value crops.
“There’s not an environment anywhere in the country that you’re not fighting something, and I think this unit could have applications in all those areas,” Newland says.