Pumping technologies optimize autogas handling
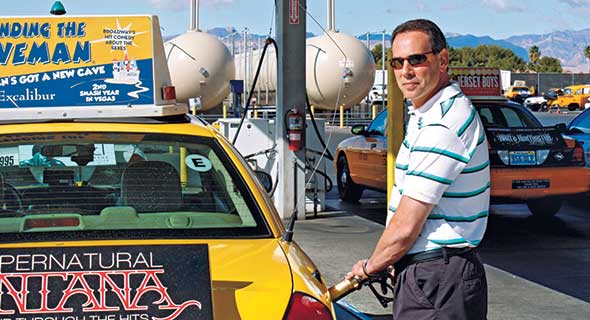
Autogas has been gaining popularity as a motor fuel because it possesses operational characteristics that are desirable to vehicle manufacturers and operators. Photos courtesy of Blackmer
For more than a century, gasoline and diesel fuel have dominated the global motor-fuels market.
Still, many meaningful attempts have been made to offer additional fuels and, today, the most popular of these alternative fuels is autogas, the name given to liquefied petroleum gas when it is used to power vehicles. Autogas has been gaining popularity because it possesses operational characteristics that are desirable to vehicle manufacturers and operators, namely that it is clean burning, high octane, abundant and environmentally friendly.
According to the World LPG Association’s (WLPGA) Statistical Review of Global LP Gas 2014, global autogas consumption in 2013 rose to 25.8 million metric tons (57 billion pounds), up 5.3 percent over 2012 and 57 percent higher than the 16.3 million metric tons (36 billion pounds) that were consumed as recently as 2003. At the conclusion of 2013, there were nearly 25 million autogas-powered vehicles in use, with almost 71,000 fueling sites located around the world.
So, while the global consumption of autogas – 3 percent of the total motor-fuels market share, according to WLPGA – still pales in comparison to gasoline and diesel, it is becoming a significant part of the motor-fuel landscape in a number of regions and countries. In those areas, retailers of autogas must utilize a pumping technology that will optimize the dispensing of the fuel.
The challenge
Autogas is a propane-butane mixture, which makes it unique in that it can be transported and stored as a liquid, but when released it will vaporize and burn as a gas. This is a property that no other commercially available motor fuel possesses.
Autogas is also a safer choice than other motor fuels because it has a narrower window of flammability. However, there are a few challenges that autogas retailers must overcome when handling the fuel:
■ As a liquefied gas, autogas must be stored in an enclosed container under pressure. When stored this way, autogas takes the form of a liquid with any gas vapors on top, which provides the pressure that keeps the liquid from boiling. Any upset in this state of equilibrium will cause the autogas to boil off or vaporize.
■ Autogas has a viscosity of 0.1 centipoise, which makes it 10 times thinner than water. This low viscosity can make autogas difficult to pump since it is harder to seal, while there is a greater risk that pump slippage will occur during transfer operations.
■ During a pumping operation, if the inlet pressure falls below the vapor pressure, vapor bubbles will form in the autogas. As the bubbles travel through the pumping chamber and pressure increases, they will implode and cause cavitation. Cavitation produces pressure spikes and results in noise, vibration and damaged pumping-system hardware.
Over the years, various types of pumping technologies have been used for the handling and dispensing of autogas. Two that have been utilized, but were found to have significant downsides in these applications, are centrifugal and side-channel pumps.
The main shortcoming of centrifugal pumps is that they are prone to experiencing vapor lock. Centrifugal pumps used in autogas-handling applications are not self-priming, unless they are submersible. An additional disadvantage with submersible centrifugal pumps is the fact that they must be degassed before maintenance can be performed on them, which is an elaborate, costly and time-consuming process.
While side-channel pumps are self-priming, they have a number of negatives that affect their ability to handle autogas. One is that they are very poor for handling any fluids that contain solids, which can be found in lower grades of autogas. Secondly, they have a high purchase price and are expensive to maintain.
The solution
A pair of pumping technologies comes to the fore when the subject is autogas handling.
Regenerative turbine pumps stand out in autogas-dispensing applications because they have been designed and built for high-pressure transfer applications. They feature an impeller design that optimizes hydraulic performance, resulting in high differential pressures even at low flow rates, which is critical for autogas applications.
The design of the regenerative turbine pump’s impeller features a rotating, non-contacting disc that has up to 60 small buckets or cells on its periphery. When the liquid enters the suction port of the pump, it is picked up by the impeller and accelerated around the narrow hydraulic channel that surrounds the cells. Kinetic energy is imparted to the liquid while circulating radially around the channel. The resultant spiraling of the liquid many times within one revolution builds energy and pressure and enhances the handling of thin liquids.
The second technology is the sliding vane pump. The secret to the success of sliding vane pumps in autogas installations is found in their unique design and method of operation.
Sliding vane pumps feature vanes that slide into or out of slots in the pump rotor. When the rotor turns, a combination of forces causes the vanes to move outward in their slots and around the inner bore of the pump casing. This forms internal pumping chambers and lets the fluid flow through the suction port and into the pumping chambers that are created by the vanes. The fluid is then transported around the pump casing until the discharge port is reached, at which point the fluid moves into the discharge piping.
Sliding vane pumps for use in autogas-dispensing applications can also feature a cavitation-suppression liner that reduces the noise, vibration and wear that can be caused by entrained vapors. Additionally, their vane design gives them excellent self-priming and dry-run capabilities, which eliminates potential pump damage.
Conclusion
Currently, the search for viable alternatives to gasoline and diesel fuel finds autogas gaining ground and becoming an even larger player in many regions of the world.
When determining which type of pumping technology to use at autogas-dispensing facilities, there are two standout alternatives: regenerative turbine and sliding vane pump technologies. These technologies have been proven to offer the operational characteristics and reliability required to successfully optimize autogas-handling operations.
Thomas L. Stone is the PSG director of marketing based in Grand Rapids, Michigan. He can be reached at tom.stone@psgdover.com.