Snuffing the static electricity spark
Whether it’s shaking hands, removing a wool sweater or walking barefoot on carpet, we have all experienced shocks caused by the discharge of static electricity. We may not always see the spark, but we sure can feel it.
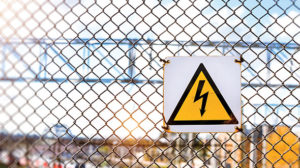
The risk of a static electricity incident increases in the winter due to lower humidity. Photo: chasdesign/iStock/Getty Images Plus/Getty Images
Static electricity is electricity at rest, but if a conductive path is present, it can result in a spark or static discharge. Sparks caused by static electrical discharges occur all of the time. They don’t cause us harm unless they occur in the presence of a gaseous vapor like propane, which can result in a fire or explosion.
It is important to understand static electricity, where and how it can arise, and how to reduce risks of a static ignition.
The risk of a static electricity incident increases in the winter due to lower humidity. When the air is dry, various materials do not retain the moisture needed to avoid the buildup of static electricity.
Static electricity can be extremely dangerous around certain propane operations. Metals, wet fabrics, wet concrete and the human body are common conductive materials. Polymeric materials such as polyvinyl chlorides (PVCs) and plastic items such as shrink wrap and plastic pallets do not retain moisture and thus can charge to extreme voltages, even in high humidity.
Even though they do not discharge sparks, non-conductors can transfer their electrical energy to something or someone that can cause a spark. This is known as induction.
Friction caused by wind blowing over plastics and other conductive materials can result in those materials carrying an electrical charge.
Take the example of an employee carrying a charged plastic trash barrel. If the employee is momentarily grounded, his or her body will become statically charged because of the charge on the barrel. After the employee puts the barrel down – and if he or she is not wearing static discharge control footwear or grounded any other way – the employee may carry the induced charge into a static discharge control area (SDCA). This is a place where propane vapors may be released or pooled – and then discharge a dangerous spark.
The smallest static spark we can see or feel (about 3,000 volts) has double the energy required to ignite propane. In other words, static electricity is a potentially invisible source of ignition.
Ways to reduce static electricity
1. Identify SDCAs – These include areas where any propane transfer, processing or storage occurs.
2. Ground yourself – Workers can conduct or carry a significant amount of static electricity as they move about the plant. Static-safe footwear or conductive wristbands and static-safe floors or floormats will discharge any buildup before employees handle propane.
3. Clothing – Never put on or remove clothing inside a SDCA. Cotton and cotton blends generate less static electricity than most synthetic materials such as nylon and polyester.
4. Housekeeping – Remove all PVCs, plastics and other synthetic materials from SDCAs.
5. Follow regulatory code – Electrical equipment inside a SDCA must be installed in accordance with NFPA 58 and state electrical codes and regulations.
6. Limit access – Limit access to SDCAs to trained propane workers who understand how to perform the particular task and handle static discharge safely.
The chances of actually experiencing a hazard caused by static electricity may be relatively small. However, the severity of such a hazard can be catastrophic. The good news is that the methods used to remediate those risks are not complex or expensive.
Stuart Flatow spent the past 18 years as the Propane Education & Research Council’s vice president for safety and training before stepping down in February 2019.
NOTE: The opinions and viewpoints expressed herein are solely the author’s and should in no way be interpreted as those of LP Gas magazine or any of its staff members.