Tuning up your bobtail for peak performance
Developing a proactive safety and maintenance culture at your propane operation is key to extending the life of your bobtail fleet.
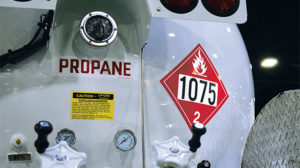
Maintaining clean and properly placed placards should be done daily. Photo by Joe McCarthy
A proactive maintenance schedule reduces operational downtime caused by equipment breakdowns, roadside inspection out-of-service orders and extended repair times on your bobtail fleet. Bobtails are valuable assets: Propane retailers need them to last longer and be safer, more productive and in service when needed. Creating a well-structured preventative maintenance program combined with a disciplined workforce is the best way to stay ahead of any issues.
Jason Soulon, a branch manager and regional sales manager from Westmor Industries, led a presentation at the 2019 Propane Expo in Atlanta on how a scheduled preventative maintenance program can protect retailers’ investments in their bobtail fleets.
Here are some key items worth adding to your regular bobtail fleet maintenance efforts:
DAILY CHECKLIST
Soulon suggests using a flashlight for areas that are not easily illuminated by the sunlight. This includes the belly of the bobtail barrel and tank rails.
- Make sure the bobtail is displaying the proper 1075 placard on each side and at both ends. Also, make sure these placards are not faded, damaged or dirty. A good rule-of-thumb is if your lights need to be cleaned, so does your placard.
- Make sure all placards are displayed horizontally to the vehicle chassis.
- Ensure “Emergency Shutoff” is clearly marked near the means of closure.
- If transporting non-odorized propane, make sure “Non-Odorized” or “Not Odorized” is marked on two opposing sides.
- Make sure all closures are closed and valves are in the “off” or closed position. Also, make sure all inlet and outlet valves are properly marked.
- Test cargo tank emergency shutoffs and off-truck remote shutoff activation devices.
- Ensure there is no noticeable damage to the cargo tank, tie-downs or tie-down fasteners.
- Ensure all cargo tank tests are current.
WEEKLY CHECKLIST
Anything that moves requires regular lubrication. That is a simple piece of advice Soulon offered to attendees of his presentation, especially when it comes to emergency shutoff levers.
- Thoroughly wash the cargo tank and equipment with a pressure washer.
- Inspect the tie-downs for corrosion, cracks and other damage.
- Inspect all surface areas of the cargo tank for corrosion and/or abrasions.
- Thoroughly inspect all piping for corrosion and/or abrasions.
- Test the cargo tank emergency shutoff. If this appears to be stiff or difficult to move, then properly lubricate or repair.
- Ensure the actuating cylinders fully open and close the internal valves without sticking, and ensure all operating levers can operate freely.
- Ensure all gauges are clear, clean and functional.
MONTHLY AND BEYOND CHECKLIST:
Keeping accurate and up-to-date records is key to any maintenance procedures, Soulon says, in case of a Department of Transportation audit.
- Remember to conduct a discharge system inspection.
- Make sure all flexible connectors are permanently marked to indicate date of installation and are less than 10 years old. Flexible connections need to be replaced every decade and must show the date they were installed and tested.
- Inspect the PTO for leaks and loose mounting hardware and the pump drive system.
- Lubricate or grease pump bearings; hose reel bearings; hose reel chain; manual rewind mechanism; hose roller rods; control system components such as switches, levers, cables and pivot points; clevis points or valve actuators; quick-spin knobs; hinges, latches, cylinders and springs of cabinets and toolboxes; and pivot points of adjustable work lights.
- Service the fluid and filters of the hydraulic pump drive system, if needed.
- Clean meter strainer.
- Replace batteries in wireless remote shutoff activation devices.
- Test and inspect the specification cargo tanks.
