California regulations lead to low-emission retrofits, new equipment
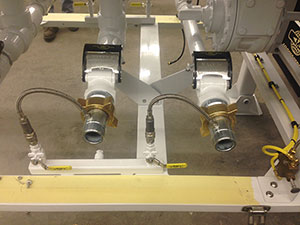
A low-emission rule on transport connectors had the industry hustling to develop needed equipment. Photo courtesy of Marshall Excelsior
New emissions regulations taking effect in California have forced the propane industry to react quickly and fast-track the development of equipment used on LP gas transports so companies can remain in compliance.
The South Coast Air Quality Management District adopted Rule 1177 on June 1, 2012, for the purpose of reducing emissions associated with the transfer and dispensing of LP gas. The extensive rule applies to the transfer of LP gas from any cargo tank, stationary storage tank or cylinder into any other cargo tank, stationary storage tank, cylinder or portable storage tank.
“The regulation for South Coast at this point requires that low-emission equipment be used throughout the entire supply chain,” says Lesley Brown Garland, president of the Western Propane Gas Association (WPGA), which has worked with the agency for about four years as it sought to develop the regulations.
South Coast initiated development of the rule in 2010, it says, because fugitive volatile organic compound emissions associated with the transfer and dispensing of LP gas were not, for the most part, accounted for or regulated by the district or the California Air Resources Board (CARB).
According to South Coast, which encompasses Los Angeles and the counties of Orange, Riverside and San Bernardino in southern California, the rule not only allows for air quality benefits but also results in potential cost savings from product losses, as well as increased safety for the industry and consumer.
Upon full implementation, the rule will reduce emissions by 6.1 tons per day from a current emissions inventory estimate of 8.6 tons per day using low-emission connector and fixed liquid level gauge technologies, the district says.
LP gas dealers and distributors will incur about 70 percent of the rule’s total average annual cost, estimated at $4.28 million from 2013 to 2025, or about $120,000 per business, South Coast notes.
WPGA is accustomed to facing such environmental regulations, as the U.S Environmental Protection Agency (EPA) keeps a close eye on California’s air quality issues. EPA looks at CARB, which looks at the local agencies to determine ways to improve air quality, Garland explains.
“In terms of education, it’s been a priority of the association at district and board meetings to talk about this issue repeatedly because we knew at some point regulations would come,” Garland says. “We are trying to be as proactive as possible about the awareness of this issue and change out equipment before we are told to change out equipment so it doesn’t fall on companies to retrofit everything at once.”
Unique situation
While the rule includes a long list of requirements and deadlines, one in particular had the propane industry hustling.
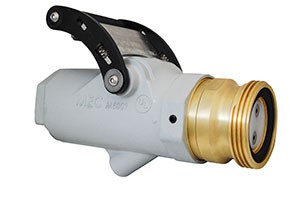
Marshall Excelsior developed a new low-emission shutoff valve in eight months.
Photo courtesy of Marshall Excelsior
The industry faced a July 1, 2013, deadline to retrofit connectors on propane transports hauling bulk propane to marketers, but no technology was available to meet the district’s emissions requirements.
WPGA was able to negotiate two extensions – first until the end of 2013 and then until July 1 of this year – as Michigan-based Marshall Excelsior Co. worked to design, test and certify a low-emission valve for transports.
“This was a more unique situation,” says Jim Zuck, director of strategic, regulatory and technical affairs for Marshall Excelsior, noting the product took eight months from original concept to build compared to a typical turnaround time of 12 months. “We would have had a segment of the industry left holding onto an issue they didn’t create.”
Marshall says it incorporated features from its ME806 valve into the new ME807 low-emission shutoff valve. In addition to transports, the valve can be used at the back of a bobtail for spray fill or at a bulk plant. The valve features a stainless steel latch for locking and won’t open until it’s squeezed and pulled. It also increases the flow rate by 360 gallons a minute.
Prior to the equipment retrofit, each disconnect could release 850 to 1,000 cubic centimeters of propane (0.22 gallons) into the atmosphere, Zuck says. The new equipment allows transport operators to meet South Coast’s revised threshold of 4 cubic centimeters per product transfer, he adds.
“We wanted to make sure South Coast didn’t come up with an arbitrary number, so we worked with the process to let them know what was feasible,” says Zuck, who was involved in discussions with the agency and its engineering staff.
“In general, if you’re willing to work with a regulatory body as opposed to already being at odds before anybody speaks, you can come up with a more amicable outcome.”
In most cases, the changeout to low-emission equipment pays for itself in lost-gallon savings, so it makes sense from a financial standpoint, Zuck says. The state’s Western Propane Education & Research Council offers a low-emission equipment rebate program. Since 2005, the propane industry has spent hundreds of thousands of dollars to help companies purchase low-emission equipment, offered from numerous industry suppliers, according to the association.
Since South Coast developed Rule 1177, at least two other districts in California are considering similar regulations, according to WPGA.
“It looks like it’s promulgating into other areas,” Zuck says.
Garland adds, “We will continue to coordinate the industry’s response to different agencies as new regulations come about.”
Summary of Rule 1177
The rule applies to the transfer of LP gas to and from stationary storage tanks, cylinders and cargo tanks, including bobtails, transport trucks and railroad tank cars, as well as into portable tanks and cylinders.
■ Requires use of LP gas low-emission connectors to limit the discharge of LP gas upon disconnection to 4 cubic centimeters or less by July 1, 2013 (extended to July 1, 2014, for transport trucks).
■ Requires that all LP gas-receiving containers be filled using a low-emission fixed liquid level gauge (FLLG) by July 1, 2017, or through use of an equivalent, alternative technique that monitors the maximum fill level without the use of a FLLG.
■ Implements a leak detection and repair program consisting of daily physical checks of connectors, quarterly leak inspections via a bubble test, and proper maintenance of vapor recovery or equalization systems on railcars and mobile fuelers.
■ Requires records of all low-emission FLLG and LP gas low-emission connector installations, leak repairs, and vapor recovery and equalization system maintenance.
■ Requires annual reports for LP gas bulk-loading facilities and LP gas transfer and dispensing facilities that offer LP gas for sale to an end user, including monthly purchase and dispensing volumes for calendar years 2013 through 2015, end-of-year inventories of all containers and associated low-emission FLLGs for calendar years 2013 through 2017, and low-emission connectors installed for calendar years 2013 and 2014 (extended for transports).
■ Exemptions provided for containers with a water capacity of less than 4 gallons, cylinders that are dedicated for and installed for use with RVs, and for facilities subject to Rule 1173 requirements.