Employee volunteers help Worthington Industries navigate tight labor market
Amid surging demand for propane cylinders and an ever-tightening labor market, Worthington Industries has tapped into its current resources and a promote-from-within culture to stem the tide of unprecedented staffing challenges.
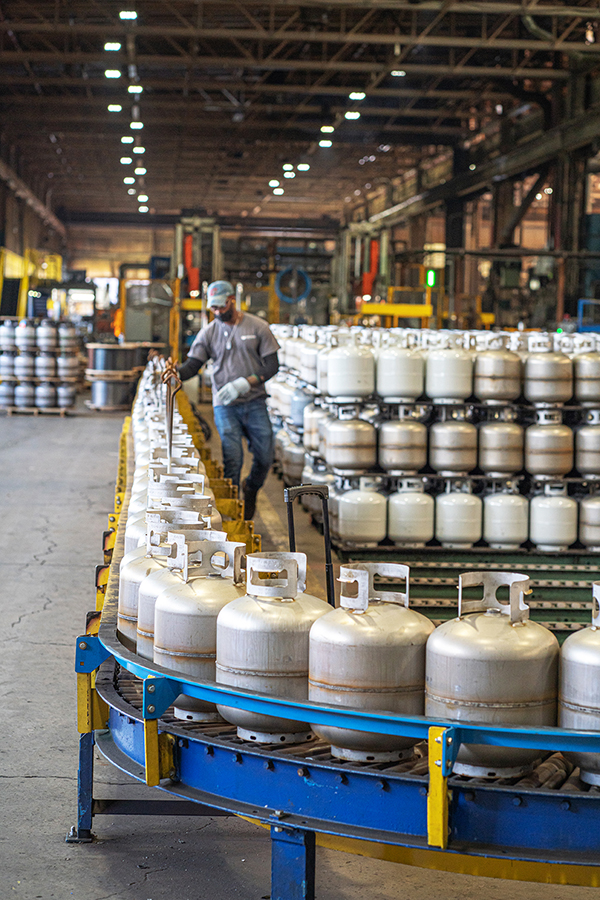
Worthington Industries employee Korey Brown prepares 20-pound propane tanks for the paint line at the company’s Westerville, Ohio, production facility. Photo courtesy of Worthington Industries
When the Columbus, Ohio-based cylinder manufacturer experienced difficulties staffing its facilities not long after the COVID-19 pandemic hit in March 2020, it sought volunteers throughout the company to fill roles on the production floor.
“We’ve been able to maintain effective staffing levels over the years. There have been times where it’s been challenging, but the pandemic had a significant impact on our demand and our ability to add staffing to meet that demand,” says Amy Thompson, senior regional human resources manager at Worthington, noting how the labor market tightened around the same time.
That left the company, including Joe Resko, vice president of operations, to inquire: Have we ever asked for help from within?
Thompson recalls Worthington making the same request more than 20 years ago during another period of heightened demand, but the impacts of a global pandemic have left many companies today struggling more than ever to keep pace with their employment needs.
Worthington shared the word via email, through its intranet and at meetings that it needed help – to support its current workforce and allow time to cross-train new hires.
“So, when we needed some help in the plant … a lot of people said, ‘Sign me up,’” says Thompson. “We had a pretty big outpouring of support.”
Learning new jobs
About 45 employees volunteered for entry-level roles on various product lines, including propane cylinder production, at Worthington’s facilities in Columbus and Westerville, Ohio.
Some worked on the weld or the paint lines. Others helped with heat treat, assembly and finishing. Each volunteer had to complete safety and on-the-job training prior to performing any role in the production facilities.
Volunteers, many of whom started their careers working on the production floor, came from numerous areas of the company, as well, including sales and marketing, finance, engineering, supply chain, transformation, human resources, new product development and innovation.
All shifts had a need, but many of the volunteers helped on day shift; a few worked the second and third shifts.
“We had at least one to two volunteers from just about every functional area that we have within the organization,” Thompson says.
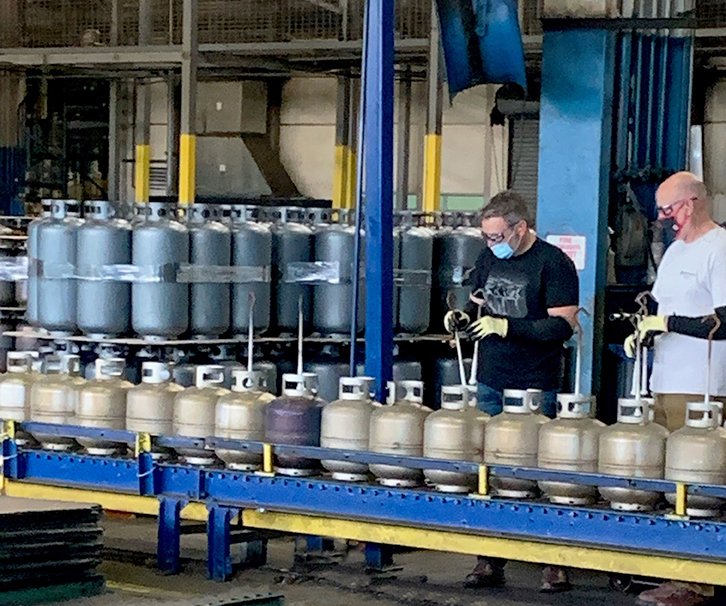
Worthington Industries’ Mark Komlosi, left, and Ken Hoffman volunteer their time in the plant. Photo courtesy of Worthington Industries
Mark Komlosi and Mike Verne, the company’s commercial leaders, were two of the first to commit their time. In addition, Jimmy Bowes, general manager, and Resko volunteered their time – and continue to do so.
“I went in with the attitude I’ll work wherever you need me,” says Komlosi, director of sales and marketing, who’s been with Worthington for the past 10 years and worked third shift in the plant while going to school full time during an earlier stint with the company. “I wanted to be shoulder to shoulder with our team.”
Aside from his volunteer role, Komlosi says he likes to visit the plants that manufacture the products he’s responsible for selling.
“I truly enjoy going to company banquets and meeting the folks who I feel like have made us what we are today,” he says. “It’s real important to me.”
Komlosi struggled to put into words his response to the many thank-yous he’s received from those within the company for his volunteer work in the plant.
“Honestly, that means more to me than I can express,” he says.
Staffing support
The volunteers did their initial work in the facilities from August 2020 through December 2020, which allowed Worthington to spend time cross-training employees.
“I wouldn’t say the volunteers went in and took over our needs to hire, but it certainly allowed us the opportunity to increase training of our new hires and current staff so that we could keep them engaged and excited about learning new jobs,” Thompson says. “When you’re understaffed, it’s difficult to cross-train, as every job is needed and we don’t have extra employees there to be able to pull someone off to provide training on something new.
“With the addition of the volunteers, it gave us some extra people in the building to be able to do that.”
Worthington’s staffing situation improved during the latter part of 2020 but again hit a difficult stretch around February and March of 2021 when the labor market tightened considerably and the company again faced employee challenges that continue today. It again sought the help of its volunteers.
“I think COVID had a lot to do with that,” Thompson says of the labor market shakeup. “People had an opportunity to make a career change because there are a lot of different opportunities available in the workforce. In addition, at the beginning of the pandemic, there were many people who decided to stay home due to fear of getting COVID.”
Meanwhile, Worthington continues to work hard and creatively to “get people in the door,” Thompson says. That includes adjustments to compensation packages, adding sign-on and retention bonuses, and enhancing its development plans with employees.
“When you do a lot for new hires, sometimes those existing employees who have been there a long time feel a little bit undervalued,” she says. “We had to make sure they were also being recognized and we were taking care of them, as well.”
Worthington also fosters long-term relationships with area high schools and vocational schools. Its Worthington Workforce Experience program gives high school seniors an opportunity to discover careers in the manufacturing industry by working on the production floor and gaining career-readiness skills training. Many students who complete the program are offered full-time employment with the company.
Plan to win
A strong workforce is needed at a time when demand and pricing have soared for products and services across industries following the COVID-19 shutdowns of 2020.
Propane cylinders and tanks are among the products sought after most by propane marketers, extending lead times and creating new challenges for buyers. Significant steel cost increases have only compounded the issue.
“We’ve had discussions with our [customers] and worked with them about looking out to the future and not handling business like they’ve historically done it – and that’s difficult, having them look out 12 to 15 months or more and forecasting their upcoming needs,” says Komlosi, noting how 20-pound cylinders, forklift cylinders and 420-pound tanks have been impacted most by the supply-and-demand complications.
“By and large, those that have planned are winning,” he adds, “and that’s kind of been our mantra – if you’re planning, you’ll be winning; you’ll have product set aside for you when you need it.”
More perspectives on staffing
Worthington Industries isn’t alone when it comes to experiencing worker shortages. Other tank manufacturers shared similar stories about a labor market that’s more challenging than normal to find and hire production talent, but they’re working to uncover solutions.
Metsa incentivizes current and future workers to grow within the company.
“We started by implementing a training incentive program for on-the-job training at each station, reshaping our internal movements policy to give priority opportunities to in-house workers and engaging with our team to have them bring about improvement projects,” says Daniel Quiroga, sales manager. “While these efforts take time to take root, we believe in our people as a driver of our success.”
Part of the challenge at Quality Steel, an LT Corp. company, is wanting to add workers to meet a strong business environment for its products. It emphasizes a positive culture of being both family and employee-owned, with a purpose of improving the lives of its employees, customers and communities.
“This, in addition to offering attractive and competitive pay and benefits, helps us attract and retain our associates,” says D.D. Hardy, national sales manager at LT Corp.
Quality Manufacturing Group realizes that companies more than ever need to value its employees.
“We’re good at making sure that someone who puts forth the effort to do the job is rewarded. We take care of our people,” says Nathaniel Simmons, quality control inspector.