Implementing employee safety practices
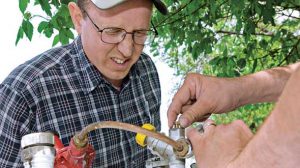
Vigilance in the propane industry means ensuring a leak test or pressure test is done and documented properly, and keeping a close watch on new personnel. Photo courtesy of the Propane Education & Research Council
I have now had the honor of representing propane industry members in claims and litigation for almost 30 years.
I have found there are, with rare exception, a good set of standard propane delivery practices that each marketer intends to employ to make the fuel safe for use. But after an accident that involves injury to life and property, there is often a disconnect between the ideals that have been set and the reality of everyday practice.
It is hard to stay vigilant, but vigilance in this industry is essential to running a business that can survive and thrive.
Small marketers are especially at risk in the event of a catastrophe. In my experience, such an event can be hard to bear for an owner and the company’s employees. It usually makes keeping insurance or finding an insurance market at a decent premium difficult, and often leads to the sale of a business.
Being proactive is its own reward – in a sense. It’s essential to keep tabs on new accounts to be sure a pressure test or leak check is done and documented properly. Keeping close watch on new service and delivery personnel is also important.
Studies show there is a high correlation between inexperience and accidents. So, make sure delivery and service personnel are shadowed for a reasonable amount of time. Employees have their own learning curve, but understand the correlation between inexperience and accidents when deciding that a relatively new employee is good to go it alone. Even employees who come in with experience should be shadowed for a period of time. This will confirm what you think they know is actually what they know.
Great recordkeeping is essential to getting it right. When a claim or lawsuit arises, the true quality of your documentation will be borne out. A periodic review of your team’s work will ensure it is done correctly. Do you review all paperwork for out-of-gas or interruption-of-service calls? If not, you should. This is the area where the vast majority of incidents arise. Do you spot check work in the field to confirm that what’s written was done? If not, consider doing so.
Doing the right thing has its own rewards. This can mean not filling a tank because something makes it unsafe or because the delivery driver is not sure. Locking off a tank with a POL lock or removing a regulator are other ways to disable the system.
At times I’ve seen servicemen or delivery drivers who are hesitant to take the steps necessary to make a system safe, or to confirm that it is safe and in keeping with company policy. As a manager or owner, you need to empower your employees on the front line to take preventive steps to stay safe. You might lose a customer or make one angry, but you may have potentially avoided an accident that carries grave consequences.
Leadership matters when creating a safety-first workplace. Employees will focus on what management and ownership say is important. Holding regular meetings that focus on a variety of safety issues at customer locations and the bulk plant help reinforce the idea that safety matters. When company leaders compliment employees for doing something that puts safety first, it goes a long way to communicating how important this is to doing a great job.
Safety is a two-way street. Great leaders are great listeners. They understand they do not possess all of the answers. They encourage all within the organization to suggest how to be better at being safe. They look to implement suggestions that work for the team and in the environment they find themselves. Most often the employees have the direct contact with customers and provide valuable information on how to get it right.
The heating season is fast approaching. As we get ready, be sure to supercharge your team to be safe out there. It will pay huge dividends.
John V. McCoy is with McCoy Leavitt Laskey LLC. His firm represents industry members nationally. He can be reached at jmccoy@MLLlaw.com or 262-522-7007.